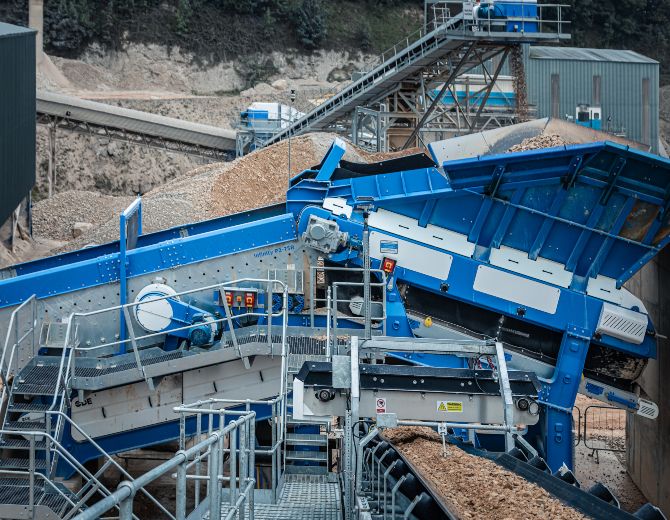
Future Proof Design
The removal of the right to use red diesel to power non-road mobile machinery and other plants in April 2022, combined with global supply issues, has resulted in unprecedented spiralling fuel costs for the construction sector. Reports from the Mineral Products Association (MPA) indicates that an additional £100 million in costs has been added to the sector.
Increasing costs are leading producers to take a fresh look at areas for savings, including updating inefficient plant equipment. While our R-Series™ primary scalping screen has been established as a market leading primary feeding and scalping screening system for wash plants, the future-proof design elements are now particularly relevant given the increased fuel costs. Design considerations include the unique, fully electric drive system delivering maximum return on investment.
The innovative construction of the VibroCentric drive also removes unnecessary weight while delivering acceleration up to 5G for enhanced screening performance. Further weight is also removed from the unique screen shaft design and patented side wall technology which eliminates welds and results in a stronger lighter screen which produces the same acceleration as traditional screens while using less power.
It now makes more sense than ever to upgrade from tracked diesel hydraulic scalpers. CDE’s Lead Product Development Engineer, Paul Quinn, describes some of the fuel savings which can be achieved by making the switch.
“A typical tracked diesel hydraulic scalper powered by engine generator will use 18 – 20 litres of fuel per hour, while the R4500, when powered by a diesel generator, will use half of this at 10 litres per hour, or 5 litres per hour for the smaller R1500.”
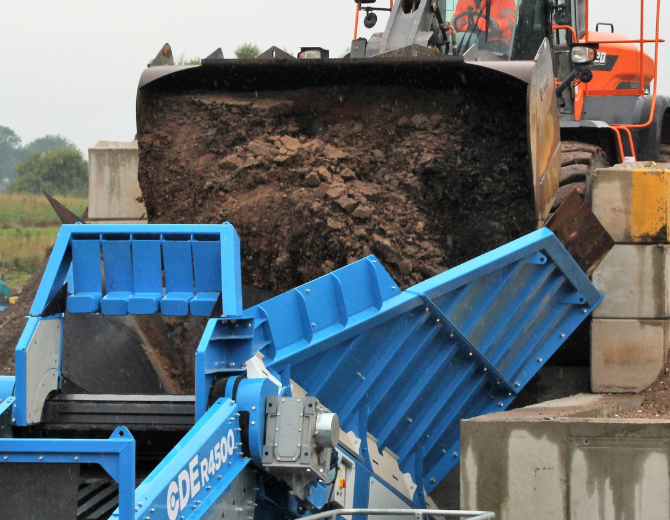
Ongoing Maintenance Costs
Another efficiency benefit to consider when looking at return on investment is on-going maintenance costs. The all-electric system which powers the R-Series requires less maintenance than a typical diesel hydraulic system and in turn reduce plant downtime.
One company who is reaping the reward of upgrading to the CDE R-Series is JA Jackson. Established in 1967, J.A. Jackson is a supplier of building materials, aggregates and ready-mix concrete as well as providing skip hire and haulage services. Working out of sites in Preston, Leyland and Lancaster, J.A. Jackson supply quarried and recycled aggregates.
JA Jackson was undertaking an overall plant upgrade project with us but and had initially intended to opt for a mobile screening unit, however during site visits to existing CDE plants Malcolm Construction and Brewster Bros, the company saw how an integrated R4500 would be beneficial to their own plant design.
Speaking about the decision, David Scott, Health Safety and Operations Manager at J.A. Jackson comments: “After visiting several cutting edge CDE sites in Scotland, we began looking at the addition of an R4500 primary scalping unit to our system.
“We were about to invest in a 20 tonne excavator and a new mobile screen which would have been costly, before adding the diesel and staff costs. The return on investment was clear, with those savings and the added benefit is that this is integrated into the plant and connects to our electricity supply.”
The ability to use clean electric power, rather than diesel generators will become increasingly important for UK operators. In June 2019, the UK became the first major economy in the world to pass laws guaranteeing an end to its contribution to climate change by 2050. The target requires the UK to bring all greenhouse gas emissions to net zero by 2050, compared with the previous target of at least an 80% reduction from 1990 levels.
David Kinloch, Director of Business Development, UK & Ireland is encouraging other operators to look for areas of their quarrying or recycling wet processing plants which could be optimised both in terms of cost savings and efficient operations.
“CDE is focussed on supporting customers to maximise their natural resources in the most sustainable way possible with greater efficient and less waste. We have continually invested in R&D to create a range of future-proof products which are now allowing our customers to make significant energy savings.”
About the R-Series
The R-Series combines a feed hopper, screen and conveyors in a variety of different configurations. The feed hopper on the R1500 has a maximum capacity of 7 tonnes when fitted with the optional extendable hopper sides while the hopper capacity on the R2500 unit rises to 20 tonnes. Both machines can be provided with either a belt feed or apron feed. The hopper has been designed to allow for feed to be delivered to the R-Series from three sides to allow maximum flexibility to cope with specific site conditions.