Tonnage
70tph
Material
C&D Waste, Excavation Waste
Output
2 Sands | 3 Aggregates
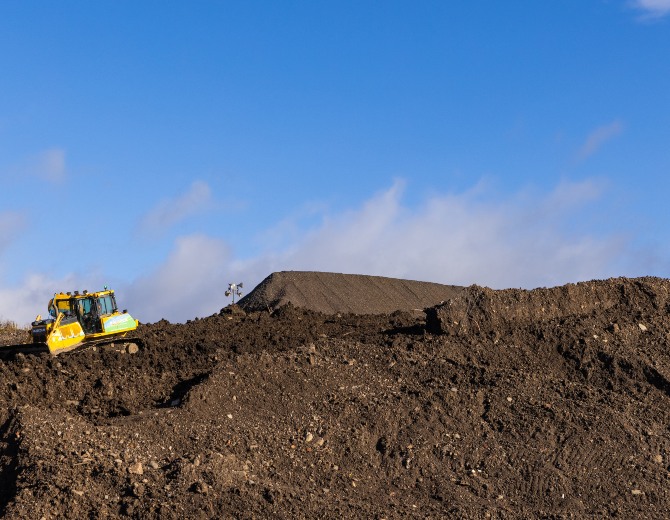
THE CHALLENGE
The processing of this material results in a recycled sand product with application in concrete and a clean recycled aggregate. "There has been significant interest in the recycled concrete sand from some of the major players in the Scottish construction materials market" explains David Balmer, Environmental Manager with Malcolm Construction. "The recycled aggregates have shown significant quality improvements from dry processed material thanks to the removal of lightweight contaminants by the Aggmax."
Originating as a family-owned business in the 1920’s, The Malcolm Group has become the leading provider of Logistics, Construction and Maintenance services in the UK. The Group endeavours to provide innovative and practical solutions, promoting the building of successful partnerships for long-term mutual gain with all stakeholders.
The Group is a forward-thinking organisation and its focus is to develop marketable and highly innovative solutions that offer flexibility to meet the challenges of the future, both commercially and environmentally, whilst preserving its heritage and values which have been built successfully from many years in business.
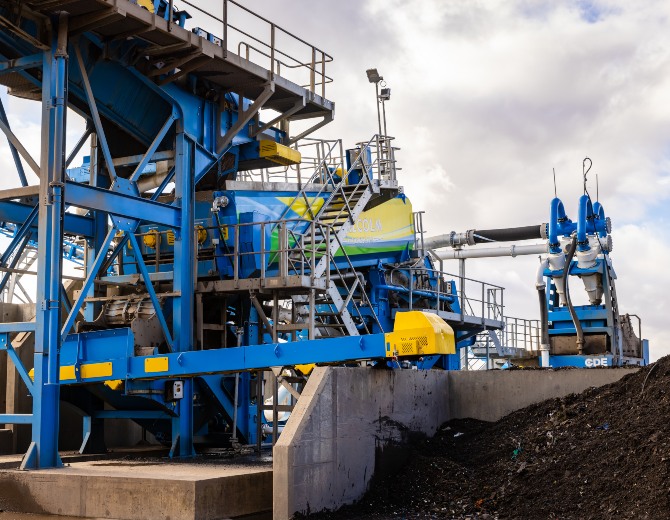
THE SOLUTION
Material is first delivered to the M2500 and an overband magnet on the feed conveyor removes any ferrous material which is subsequently discharged to a skip. A wash box at the head of the feed conveyor fluidises the material before it is delivered to the integrated Prograde P275 double deck rinsing screen.
Once the aggregates have progressed through the Rotomax logwasher they are discharged to the dewatering and sizing phase. In this instance a triple deck dewatering screen is employed to allow for the production of a 5-10mm, 10-20mm and +20mm recycled aggregate which are sent to stockpile via three 15m mobile conveyors. The configuration of this dewatering and sizing phase can be altered with the option of single deck, double deck or triple deck screen.
The option chosen will depend on a variety of factors including the aggregate specifications required and existing equipment available on-site. "If there is an existing mobile dry sizing screen on-site this can be employed at this stage allowing for specification of the single deck dewatering screen on the Aggmax" explains David Kinloch, Business Development Director for UK & Ireland at CDE. "The advantage of the two or three deck screen is that it can save considerable space on site by removing the requirement for an additional dry sizing screen."
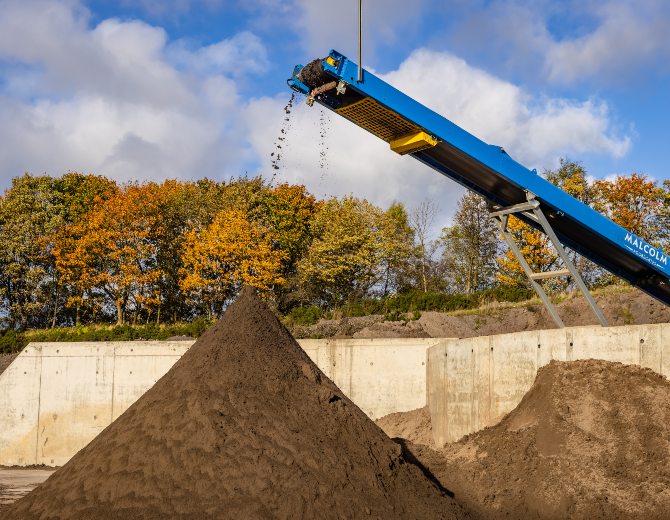
THE RESULTS
A 0-5mm sand is dewatered and stockpiled while the 0-2mm material is collected in the Evowash sump and pumped to the hydrocyclone. The -63micron fraction is removed along with the waste water via the cyclone overflow and is sent to the water treatment phase. Meanwhile the fine sand fraction is discharged via the cyclone underflow onto the second side of the split Evowash screen before being dewatered and stockpiled.
The was plant produces a 0-2mm and 0-5mm recycled sand, and 5-10mm, 10-20mm and 20+ mm recycled aggregates which are used in a variety of construction projects and in the development of production material.