Tonnage
200tph
Material
C&D Waste
Output
0-2mm & 2-4mm Sand, 4-6mm, 6-10mm, 10-20mm, 20-40mm and 40-80mm Aggregates, +80mm oversize and filter cake
Established in Liverpool in 1986, CCC Waste has grown to become one of the largest recycling and waste management operators in the North-West of England. Committed to environmental best practice, the haulage and excavation firm recently partnered with wet processing experts CDE to commission a cutting-edge waste recycling plant to help it achieve its ultimate aim of zero waste to landfill.
In the Liverpool area, construction & demolition (C&D) waste is in abundance and CCC Waste, an established market leader in total waste management solutions, was processing over 15,000 tonnes of recycled materials every week.
With such waste volumes readily available, the company, operating from its 35-acre site in Kirkby, recognised than a modern technological solution was needed in order to close the loop on construction waste.
“We process a large variety of waste, from C&D waste to that generated by households, including plastics, card, and so much more. Much of these streams contain recyclable materials. In particular, recycled aggregates are a large part of our business and an area where we see great potential for further development in pursuit of our zero waste ambitions.”
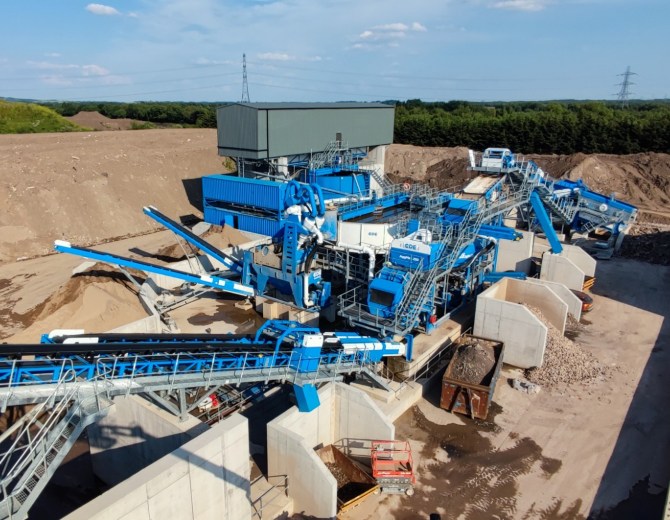
The Challenge
Operating a dry crushing and screening plant, the company faced challenges when processing damp materials during the wet months of the year, which resulted in more frequent downtime and lower product yield as a proportion of the hard to process material would be sent to landfill – an undesirable outcome for a company steadfast in its commitment to advancing the circular economy.
“When we were dry processing we couldn’t extract any sand; it was all mixed up with soils and we couldn’t get any of the sand out. Anything –50mm down was going to landfill,” Munro said.
CDE business development manager Mike Bibby said a full technical solution was required to support CCC Waste to gain momentum in its mission to achieve 100% landfill diversion.
“It was evident that many of the downstream challenges around product quality, specification, and waste to landfill volumes, to name a few, were stemming from inefficiencies in the dry crushing and screening process.”
A wet processing solution, he said, would “maximise the recovery of washed recycled materials, which can be marketed at a premium, while eliminating associated disposal charges and delivering significantly for the business, both environmentally and commercially.”
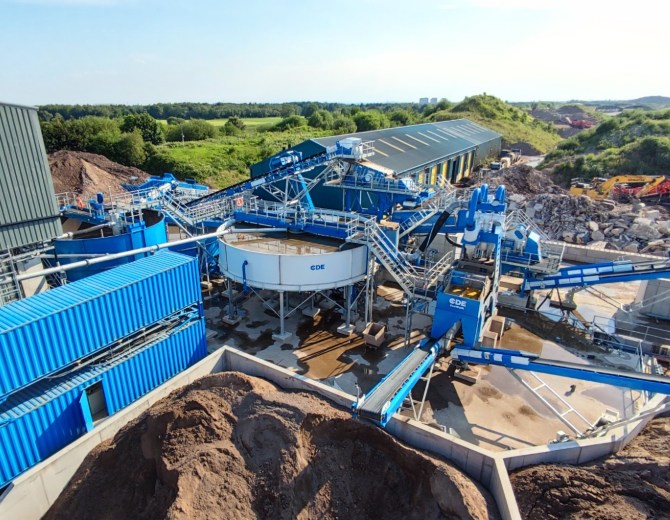
CDE and CCC in sync
Working in close partnership, CDE and CCC Waste set out on journey to define a solution aligned with the needs of the business, which included visits to reference sites throughout the UK, such as Malcolm Group, William Thompson & Son, and Sheehan Group, where CDE plant equipment is in operation.
“We had been looking to invest in washing equipment for quite some time and we explored several different options, but it was important we find the right partner – one whose values aligned with ours,” Munro said.
“We visited several CDE sites in England and Scotland and those visits were hugely valuable to us. The plants were operating with great efficiency. We came away with ideas about how we could maximise the footprint of our own site, too. They helped us see the synergies between our two businesses.”

The Solution
Guiding CCC Waste as it took its first steps into the wet processing of materials, CDE proposed a solution comprising its R4500 primary scalping unit, which is ideally suited to handle the challenging and variable nature of the company’s incoming C&D waste streams from across a broad range of industries.
A flexible and responsive plant that can cope with a wide variety of feed material, the solution features CDE’s AggMax™ scrubbing and classification system, which allows for the effective removal of organic material and other contaminants prevalent within CCC Waste’s feedstock, and the EvoWash™ sand washing system, complete with patented Infinity™ dewatering screen, which offers unrivalled control of silt cut points to guarantee high-value, in-spec sands that are ready for the market straight from the belt.
The inclusion of the AquaCycle™ thickener for primary stage water management and a Filter Press ensures CCC Waste is able to recycle up to 95% of the process water for immediate recirculation and reuse, while producing a filter cake by-product with a range of applications to help achieve complete landfill diversion of incoming C&D waste.
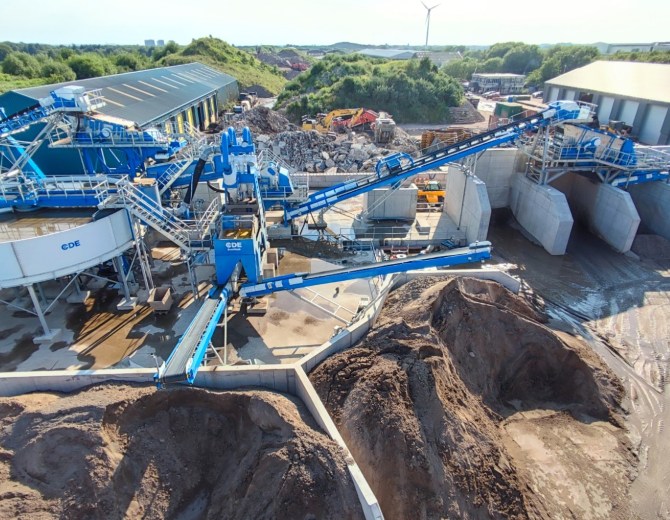
The Result
Commissioned late last year, the new CDE plant has doubled sand and aggregate output for CCC Waste. Every week, Sean and his team are now producing up 30,000 tonnes of washed recycled construction materials. The plant is currently processing up to 200 tonnes per hour and producing nine graded products, including sand and aggregates ranging from 0-2mm up to +80mm oversized as well as a filter cake.
“We were sending so much to landfill. The CDE plant has completely transformed our business, so much so that we’re even collaborating on a project to develop a concept brick from the filter cake by-product that requires no heat to cure and is low energy. The idea is scalable, sustainable, and really aligns with our long-term environmental vision. It means we’re diverting 100% of our construction, demolition, and excavation waste from landfill,” Munro commented.
Reflecting on the success of the partnership CDE’s Mike Bibby added, “Landfill diversion was the name of the game, but this project goes much deeper. Every aspect of the solution designed and engineered by the CDE team circles back to Sean and his team’s overarching vision. Material is being recovered on a large scale, and operationally that process is more sustainable than ever before. Overall carbon footprint at CCC Waste is down, thanks to the transition from diesel to our all-electric drive.”
Providing local customer support, CDE’s CustomCare team will continue working with CCC Waste to ensure the business achieves and maintains optimum efficiency throughout the lifetime of the plant.
“The level of aftercare support CDE has committed to delivering was important to us. It gives us reassurance and cements the partnership. We’re both driving change in the waste recycling space and the team is truly invested in our success,” Munro concluded.