Tonnage
950tph
Material
Iron Ore
Output
Iron Ore (silica and alumina reduced from feed material increasing Fe content to over 60%)
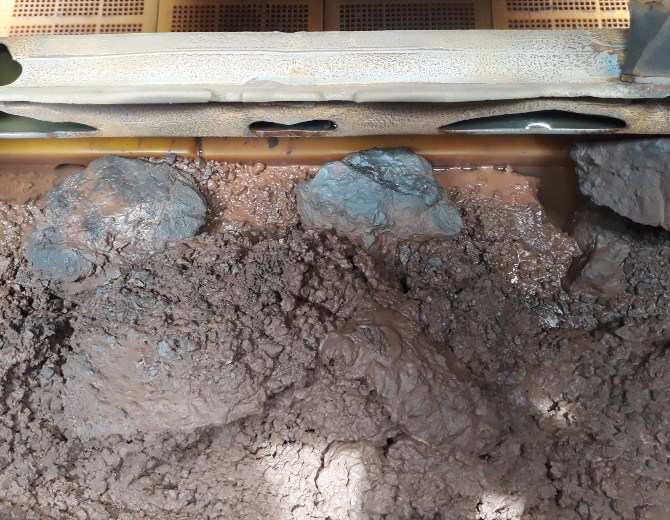
THE CHALLENGE
CDE undertook its largest mining project to date in late 2016, converting almost 18 million tonnes of lowgrade iron ore into saleable product for SIMEC in South Australia.
SIMEC required an advanced turnkey washing solution to beneficiate extremely abrasive haematite held in stockpiles of low-grade iron ore which had accumulated over years of mining of the Iron Monarch, Iron Princess, Iron Empress, and Iron Baroness deposits.
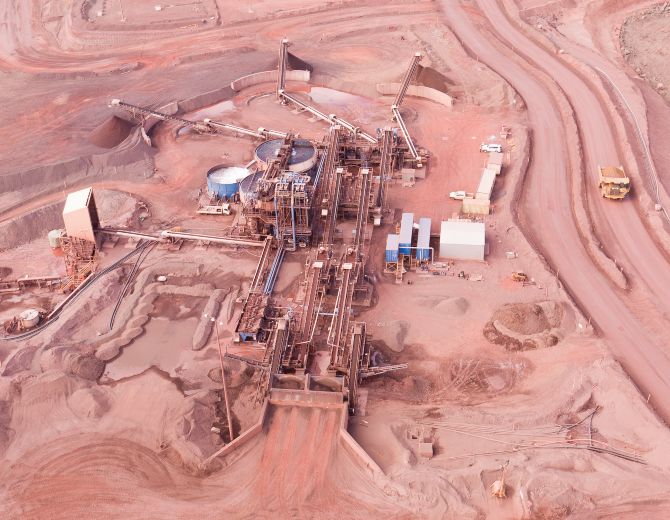
THE SOLUTION
The plants beneficiate a low-grade ore that was historically considered waste material. This is achieved by removing silica and alumina from the feed material, as well as gravity separating low-grade from high-grade ore. Silica levels, which range from 14% to 20%, have reduced to 6.4% after processing. Alumina levels range from 5.9% to 8.8% and are reduced to 2.8% after processing.
The iron ore wash plant also removes clays from the feed material and the combined effect means the Fe content increases from between 43.4% and 52.7% in the feed to above 60% iron ore product, with a yield of up to 50%. The plant consists of an initial washing and screening stage using CDE’s M-Series™ modular range equipment followed by scrubbing of the coarser fraction by RotoMax™ log washers.
There then follows a dry screening utilising our patented Infinity Screen™ range prior to gravity beneficiation in the course and fine jigs, dewatering and conveying to stockpiles via more than 20 CDE conveyors across two processing plants.
The finer fraction is further washed and separated prior to being de-slimed in cyclones at 200 Mesh and gravity beneficiated through a series of spirals banks. Three of CDE’s A1500 AquaCycle™ thickeners are deployed across the two plants to form a concentrated tailings sludge and recycle process water.
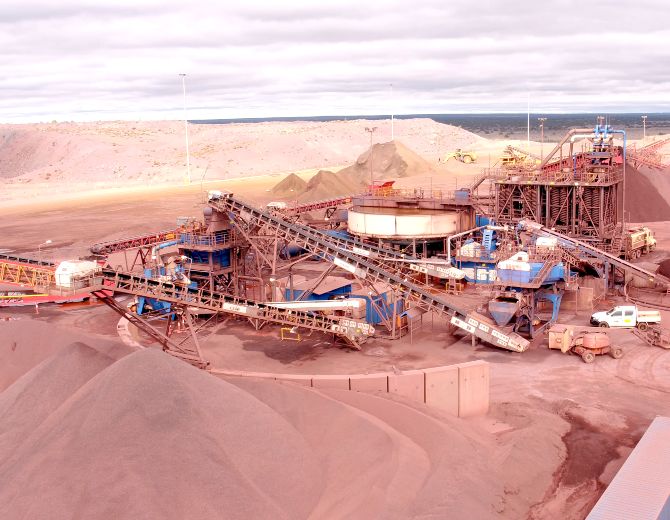
THE RESULTS
The two wet processing plants at Iron Knob and Iron Baron, with a combined throughput of 950 tonnes per hour, were designed, manufactured and delivered within 18 months from signing - which was unprecedented for an Australian mining project of this nature.
The two CDE installations have been performing with exceptional attrition levels delivering significant ROI on a low-grade, low-value waste iron ore feed product, which is upgraded to a high-grade valuable 60-63% Fe ore.
Since commissioning, it has injected an estimated $25million (AUD) into the local economy and secured important employment opportunities.
Award Recognition
In 2019, CDE achieved a double award recognition for the project, first picking up the coveted Geoscience Ireland Award at the 2019 Engineers Ireland Excellence Awards. This was followed by CDE collecting the hotly contested award for Innovation Productivity Improvement at the 2019 Premier’s Awards in Energy & Mining, hosted by the South Australia Department for Energy and Mining in Adelaide.