Tonnage
150tph
Material
Claybound Aggregates, Limestone, Crushed Rock, Sand & Gravel
Output
2 Sands | 2 Aggregates
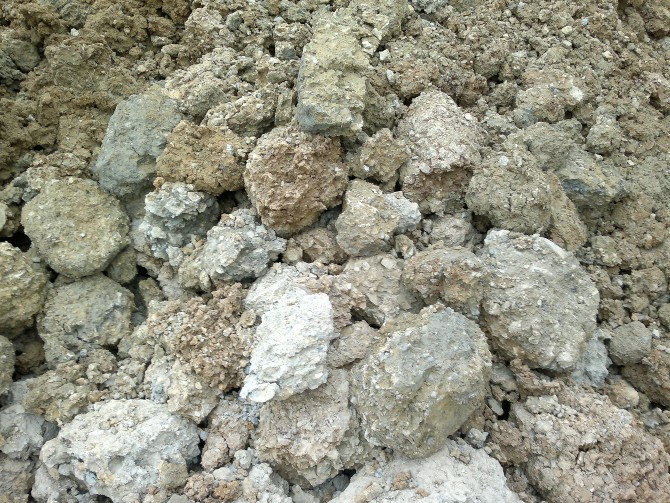
THE CHALLENGE
Kopalnie Dolomitu is one of the largest suppliers of aggregates in Poland with a focus on a sustainable approach to mining. “As a company we are driven to ensure that we utilise the resources under our stewardship in the most sustainable way possible” explains Mr Przemyslaw Bokwa, Managing Director at Kopalnie Dolomitu. “We achieve this at Bokwa by extracting maximum value from the material through the introduction of the most efficient processing system available while also minimising environmental impact through efficient use of the water used to wash the material.”
The highly plastic nature of the clay at Jurkowice quarry means that it is extremely hard to break down and without the introduction of a washing plant the resource at Jurkowice would have been sterile.
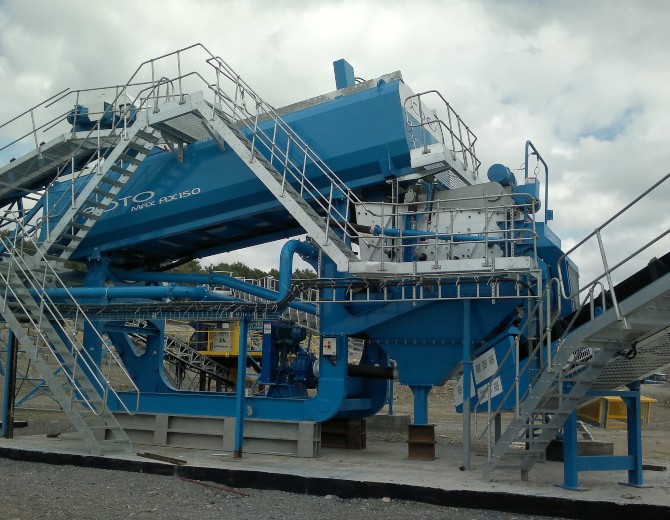
THE SOLUTION
In order to effectively tackle the clay present within the feed material CDE introduced two AggMaxTM modular logwashers. “It was not only the amount of clay present but the nature of the clay which ensured that scrubbing through two AggMaxTM systems was required” explains CDE’ Sales Manager for Europe.
The washing plant operates at 150 tph and has two different feed materials, 0-8mm and 0-63mm. The material is loaded by dump trucks into two feed L55 feed hoppers specifically designed for the sticky nature of the feed material. Material is discharged from the feed hoppers onto a feed conveyor before being sent to the first AggMaxTM 151S Modular logwasher.
A CDE vibrating finger screen removes any +80mm material that could be present before the feed material enters the first Rotomax RX150 logwasher where attrition is delivered by 120 paddles mounted in a spiral arrangement on the dual shaft machine. The 0-2mm sand fraction liberated by the Rotomax is discharged with the wastewater and sent to the EvowashTM sand washing plant. Meanwhile the 2-63mm material is dewatered on the integrated EvoScreen before being sent via transfer conveyor to the second AggMaxTM 152. Once the material has been scrubbed by the second AggMax the 2-16mm material is delivered to a ProGrade P2-75 screen where aggregates are then classified into 2-8mm, 8-12mm and 12-16mm. Meanwhile the 16-80mm material is sent to a VSI Crusher before being returned to the circuit between the two AggMaxTM machines.
In addition to the AggMaxTM logwashers and the EvoWash sand washing plant, the installation also features a full closed circuit water recycling system including the AquaCycleTM A600 high-rate thickener and GHT Filter press. The wastewater containing the 0 to 63 micron fraction is delivered to the AquaCycleTM while, the settled sludge is discharged to a concrete buffer tank before being sent to the filter press. This ensures the maximum amount of water is removed from the filter cake and re-circulated into the washing plant, therefore reintroducing up to 96% clean water to the washing plant.
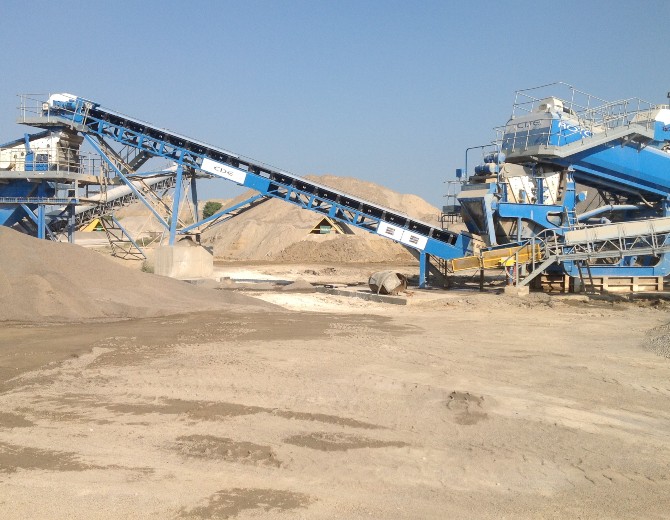
THE RESULTS
The new plant delivered by CDE, in conjunction with sales partners in Poland Biuro Handlowe Ruda, produces 4 output products used in a wide range of applications including road construction and residential, industrial and commercial building projects. Commenting on the new processing system Mr Przemyslaw Bokwa says “The introduction of our new limestone washing plant gives us a competitive edge due to the quality of the sand and aggregates we can now produce.”