Tonnage
90tph
Material
Other Minerals & Ores, Alluvial Gold
Output
Alluvial Mining of Precious Metals
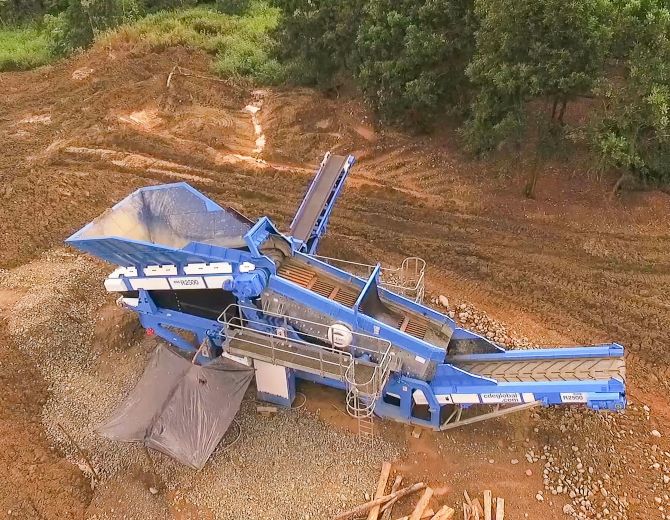
THE CHALLENGE
The land where AuVert is executing its operations is rich in precious metals, formerly mined for platinum, the old operation did not fully maximize the resources onsite and so precious metals remain in the ground, something AuVert wanted to capitalize on with its new wet processing plant.
AuVert’s focus first and foremost is the extraction of remaining precious metals but there is also a social and environmental dividend. Its work rehabilitates used land for agricultural purposes, creates employment and benefits the local economy through engagement with neighboring suppliers.
AuVert is working with the local community to remediate the ground, creating fairly-paid jobs and in turn safeguarding the welfare of those living in the area. This work is not without its challenges, and AuVert needed a technology solution that would deliver a rapid return on investment.
Due also to their remote location, this technology needed to suit the environment in which they operate. AuVert therefore opted for a provider that could deliver a modular solution to meet its goal of operating a profitable short term rehabilitation project followed by relocation of the wet processing plant.
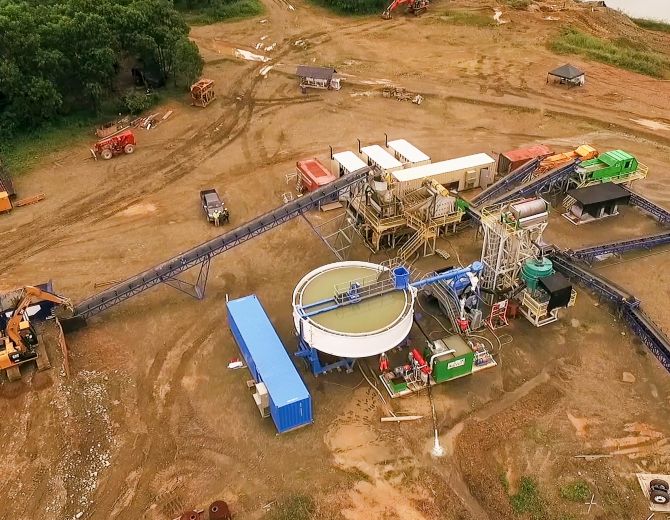
THE SOLUTION
Combining AuVert’s technology with CDE’s experience in dewatering and tailings management, the solution allows for the extraction of the remaining precious metals existing in the ground, while removing up to 93% of residual mercury which has to date prevented this land from being used by the local population.
Rafael Milani, Technical Engineer for CDE’s global mining division explained, "This was a unique project in that not only did AuVert require a provider with whom it could collaborate to achieve the ideal modular wet processing solution to make its mining operations as efficient as possible, but it were committed to a longer goal of returning the land in a suitable condition for agricultural purposes and also required the flexibility that CDE’s modular approach offers to allow relocation of the plant to other remote locations.
We needed to understand AuVert’s plant and site, its business needs and vision, and the AuVert team were thorough in guiding us.”
Collaboration and Preparation
AuVert was in need of an innovative solution to complement and support its visionary work. Prior to starting the design of the plant, CDE embarked upon a fully collaborative and consultative approach to the project.
Milani continues, “This project holds the true essence of a partnership. We took the lead from AuVert, appreciating its detailed brief and expert knowledge of the landscape and challenges the plant would face. We worked together to develop a unique solution that would unlock the full potential of AuVert’s resources, whilst also providing the ability to repurpose the plant at the end of the project...”
James Slade CEO for AuVert Mining Group said, “We have a long history of being an ecologically conscious company – eco-friendly and efficient alluvial mining is at our core, pioneering sustainable mining and environmental remediation of legacy mine sites in collaboration with local communities is what drives us. We knew that CDE’s technology combined with our own knowledge and existing operation could result in maximized outputs and achieving return on investment in a sustainable way.”
Robust screening application
At the front end of the process AuVert employs the world-class R2500, a durable hopper, feeder and scalping screen which conditions the feed prior to further processing by breaking down tough clay bound materials and scalping large boulders to provide a consistent feed to the processing plant and optimize production throughput.
The CDE feed hopper capacity allows for charge filling which has the potential to free up an operator and vehicle, ultimately reducing the level of operator intervention required at the Condoto site.
The modularity of the R2500 provides a huge advantage to the customer – allowing it to be easily moved and relocated around the site such that large volume of reject scalpings do not need to be transported to the plant. Reduced volume of prepared feed mean that trucking volumes and fuel consumptions are lower.
Featuring CDE patented Infinity screening technology, which eliminates welds and creates a stronger, lighter screen, the R2500 produces the same acceleration as traditional screens while requiring less power, resulting in longer lifetime and reduced running costs.
Leading wet processing engineering
The tail end of the process features CDE’s flagship AquaCycleTM thickener – a compact, modular materials washing system which integrates a high frequency dewatering screen, sump and hydrocyclones to provide unrivaled control of the slimes cut point.
Environmental awareness and commitment to sustainability dictates the implementation of resource saving strategies – a mission embodied by the combined AuVert-CDE plant. By this stage of the process, precious metals have been extracted and residual mercury removed. The EvoWash then deslimes and dewaters the tailings, while simultaneously creating valuable materials which can be redeployed to the construction market.
The EvoWash also incorporates patented Infinity Screen™ technology for optimal dewatering results and is a favorite with the operators at the AuVert Mining site for its superior reliability.
THE RESULTS
The AquaCycleTM water management system recovers up to 90% of the water used throughout the process, as a result, on average, the CDE and AuVert approach uses 77% less water than traditional methods without using any toxic chemicals. This ensures the water supply won't end up contaminated and unsafe for the neighboring community. The AquaCycle and EvoWash technology has also provided flexibility to enable the plant to process variable clay bound feed material with a high percentage of fines.
Combining AuVert’s technology with CDE’s experience in dewatering and tailings management, the solutions employed at the Condoto site allows for the extraction of the remaining precious metals existing in the ground, while removing up to 93% of residual mercury which has to date prevented this land from being used by the local population.
As a result, the mine site now bears great hope for the community, creating jobs for the local people during and after the mine life and rehabilitating the land for future agricultural use. Operated in partnership with the people of Condoto, the plant greatly contributes to the prosperity of the region, providing a vital platform for economic growth. AuVert also brings a number of important Corporate Social Responsibility initiatives to the region, not least funding musical instruments for local school children.
Aside from the direct impact of creating jobs on site and supporting local business, the community has already seen a reduction in crime levels in the area. Profit from the operation is invested back into the community, aiding education in schools and providing vital sand and aggregates for construction materials from the washed products on site.
Going forward, CDE is working closely with AuVert to introduce their technology to additional plants. Having learned more about the processes due to AuVert’s expertise, the company looks forward to expanding their provisions and to collaborating on further projects with their joint commitment to a New World of Resource firmly at the fore.