Tonnage
200tph
Matériel
Sables Siliceux, Sable et Graviers, Récupération Des Ultra Fines, Sables De Sports
Production
Ultrafin (30-150 microns) | Sable de Verre (150-650 microns) | Sable grossier | (650 microns-3mm) | Surdimensionné (3mm)
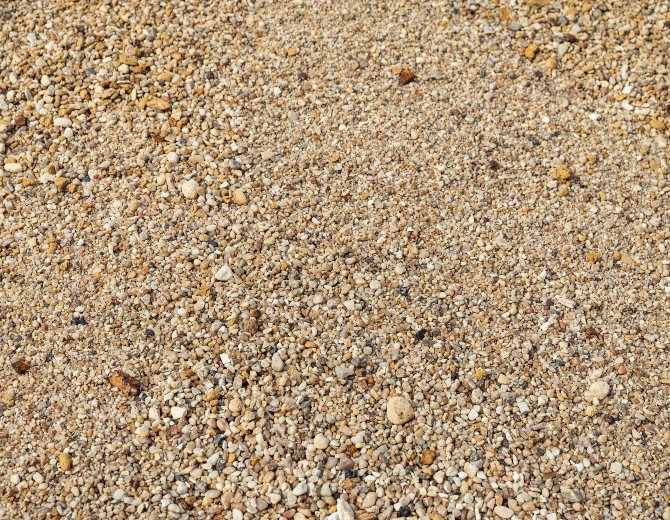
PROBLÈME
SMETRAM, une filiale du groupe Sebri, exploite les carrières de sable en Tunisie depuis 2001 et dessert principalement le marché national, en particulier les centrales à béton et l’industrie de la construction en général. Pour accroitre son portefeuille d’activités, la compagnie a décidé d’investir dans la production de sables industriels d’une granulométrie spécifiquement adaptée aux spécifications de l’industrie du verre en Afrique du nord et en Europe, en se concentrant sur le traitement et la valorisation de sable siliceux dans la région de Oueslatia. Le marché du sable de verrerie, en particulier du sable de verre plat, requérant l’adhérence à des normes qualitatives très élevées, la société avait besoin d’équipements de traitement à la pointe de la technologie et capables de gérer une quantité d’extraction quotidienne de 3 000 tonnes de sable tout en résistant au temps et à l’usure.
Le dossier
SMETRAM souhaitait étendre ses opérations à la production de sable de verrerie, accompagnée d’un éventail de produits annexes (sable industriel et farine de silice) pour en augmenter la valeur commerciale en éliminant les contaminants par un processus de lavage et en affinant les points de coupure pour une meilleure qualité des produits finis. La société souhaitait également avoir l’option de produire une fraction de 30-150 micron qui rendrait son offre unique dans la région.
M. Habib Sebri, PDG de SMETRAM, explique : «Avant de nous lancer dans le sable de verrerie nous exploitions le site de Oueslatia pour la production de matériaux de construction. Cependant, il était clair que le matériau siliceux du site, d’excellente qualité, présentait une opportunité de développement intéressante dans le domaine du sable pour les applications de verre plat en particulier.
«Au moment d’investir dans des équipements de traitement de sable qui garantiraient la réussite du projet, nous n’avions pas droit à l’erreur. À la suite d’une recherche exhaustive des différentes options à notre disposition, nous avons choisi une solution modulaire de traitement par voie humide de CDE.
«La pertinence de l’équipe commerciale de la société, son investissement dans l’innovation et les nouvelles technologies, ainsi que la qualité des matériaux utilisés ont été un facteur déterminant dans notre décision.»
La carrière de SMETRAM n’étant jusqu’ici dotée que de peu d’équipements, la société tunisienne et CDE ont pu développer une solution de lavage sur mesure et sans contraintes d’espace autre que la surface naturelle du site. Un processus de co-création a permis aux ingénieurs de CDE de travailler avec le client pour développer une installation de traitement par voie humi
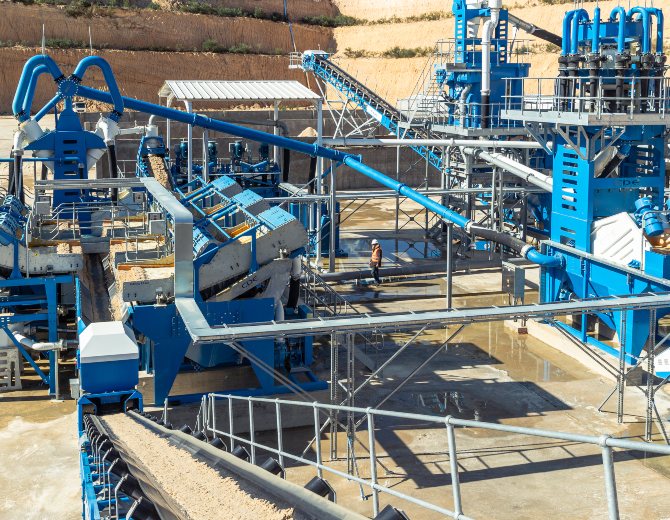
SOLUTION
Pour garantir la précision des points de coupure du sable ainsi que les volumes de matériaux requis, SMETRAM a opté pour une solution de lavage complète clé en main CDE pour traiter jusqu’à 200 tonnes par heure de sable de silice et produire 100 tonnes par heure de sable fin pour l’industrie de la verrerie ainsi qu’un éventail de matériaux annexes. L’installation de lavage comprend une combinaison d’équipements CDE opérant en parfaite synergie: une station de lavage M4500 – d’une capacité maximale de 450 tonnes par heure – incorporant des cribles de séparation haute fréquence Infinity™, quatre cellules d’attrition, des séparateurs à spirales, un système de séparation densimétrique par classification à contre-courant (CFCU), des nano-cyclones, quatre unités de lavage EvoWash™ pour traiter les matériaux fins, le sable grossier, pour éliminer les contaminants et pour la production de sable de verre respectivement.
L’efficacité du système est renforcée par l’action d’un clarificateur AquaCycle™ pour le recyclage des eaux de process. Au cours de la conception du projet, SMETRAM a choisi d’augmenter la capacité de l’AquaCycle de 900 m3 à 1500 m3 et d’ajouter une trémie à l’installation.
Une technologie de pointe
Des points de coupure d’une précision inégalée
L’unité de traitement de matériaux par voie humide M4500 est rapidement devenue très populaire auprès des clients de CDE depuis son lancement en 2014. Cette installation haute technologie est compacte, puissante, simple d’utilisation et économique. La technologie cyclonique de CDE utilise la force centrifuge pour la classification des matériaux plutôt que la gravité, ce qui permet de conserver chaque grain de sable viable dans le système, minimisant la taille ainsi que les besoins d’entretien des bassins de décantation. La conception du cyclone permet également d’établir un nombre de paramètres variables pour obtenir une précision de points de coupure inégalée. Pour renforcer l’efficacité du processus de traitement, le système d’attrition et de spirales réduit la contamination en fer.
Bassem Idriss, Chargé de Projets pour la région Europe et MENA à CDE explique : «La station de lavage de matériaux M4500 démontre l’efficacité de la technologie cyclonique de CDE et la capacité d’adaptation de nos équipes process et ingénierie, qui ont su adapter le traitement à la demande de SMETRAM pour produire un sable de verrerie de très haute qualité.
«Les hydrocyclones ont été construits selon les besoins spécifiques du client, basés sur les analyses du produit d’alimentation menées directement par le laboratoire de CDE durant la phase d’avant-projet.
«L’eau de process, chargée des fines indésirables, est évacuée au niveau de la surverse des cyclones tandis que le sable traité, ainsi valorisé, continue sa course pour entrer en phase d’essorage et de déstockage. Bénéficiant de points de coupures d’une précision incomparable, les produits sont traités conformément aux normes requises et sans risque de mélange.»
Une gestion optimale de l’eau
L’installation de SMETRAM comprend une unité de traitement de l’eau de process – un clarificateur AquaCycle CDE d’une capacité de 1500m³/h – qui permet de recycler jusqu’à 90% des eaux usées par un système de blocage des fines et d’expulsion des boues dans un bassin de décantation.
Idriss continue: «En Tunisie, un pays chaud et sec, il est important de prendre en compte les difficultés d’accès à l’eau fraiche. Il est essentiel de ne pas gâcher une goutte d’eau. Le clarificateur AquaCycle de CDE permet à SMETRAM de recycler l’eau de process en circuit fermé pour une réutilisation immédiate dans le système.
Les eaux usées, après leur passage dans la chambre de désaération et après avoir été au contact de l’injection de floculant, passent au centre du clarificateur pour que le travail de la floculation opère et agisse sur la sédimentation des fines. L’unité de floculation intégrée au système permet le dosage précis de floculant pré-mélangé pour une décantation efficace. Un moteur unique entraîne les bras-râteaux de l’AquaCycle pour un traitement optimal des boues avant leur évacuation.
On ajoute à l’eau clarifiée un appoint d’eau au travers d’une unité AquaStore CDE. Cet appoint très modéré sert à couvrir les pertes en ligne dues aux humidités résiduelles du sable et des boues. On renvoie alors le tout immédiatement en direction du process qui fonctionne ainsi quasiment en circuit fermé. La section conique du clarificateur, équipée d'une pompe à boue intégrée, permet une installation et une mise en service rapides.
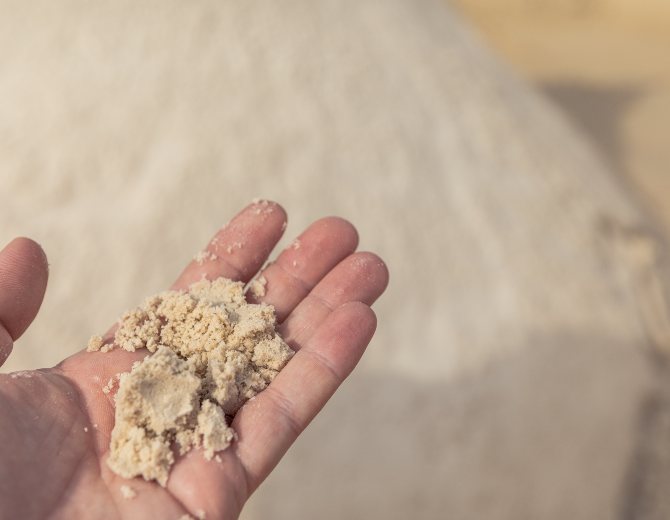
RÉSULTAT
L’installation CDE pour SMETRAM recouvre 90% du produit d’alimentation, le transformant en cinq produits sous spécification de haute valeur commerciale. Elle produit du sable de verrerie (150-650 microns) et des produits annexes : des surdimensionnés (3mm) prêts à être utilisés dans les systèmes de filtrations des eaux, du sable grossier de 650 microns-3mm prêts à être broyé pour faire la farine de silice, des ultrafines (30-150 microns) pour la céramique ou autres industries, et du sable riche en fer qui peut être utilisé dans les terrains de sport . Présentant un taux d’humidité typique de 12% à la sortie du système, les matériaux sont produits simultanément et prêts à la vente sans nécessiter de temps de séchage supplémentaire.
M. Sebri commente :Notre solution de traitement CDE a changé la donne dans l’industrie du sable de verre en Tunisie et sur le marché nord-africain dans son ensemble. Elle représente la technologie la plus avancée disponible sur le marché nord-africain et nous a permis de devenir ultra-compétitifs au sein d’une industrie dont les standards de qualité sont extrêmement élevés.
Notre sable de verrerie est vendu pour la production de verre blanc, et les autres fractions sont vendues pour des applications industrielles diverses. Notre retour sur investissement est rapide grâce à la puissance et à l’efficacité de la solution de traitement CDE.
Nous avons réussi à augmenter notre offre et à nous positionner sur de nouveaux marchés, ce qui a renforcé la réputation de qualité et de consistance de service de SMETRAM auprès de ses clients.
Quand le sur-mesure prend tout son sens
Les équipements CDE sont conçus et construits dans les usines de la société pour s’adapter aux circonstances de chaque site de manière à maximiser la qualité et quantité des matériaux produits. Dans le cas du site siliceux de SMETRAM, les types de produits finaux demandés requéraient un concept d’ingénierie extrêmement précis.
L’équipe de CDE a ainsi, en collaboration avec le client, conçu une installation sur mesure, capable de produire simultanément cinq produits de granulométries différentes sans risque de mélange pour ne pas compromettre leur qualité et consistance. Les ingénieurs de CDE travaillent avec la devise de la société à l’esprit, un Nouveau Monde de Ressources, pour atteindre un objectif de ‘zéro déchet’ sans gâchis d’eau. CDE offre un éventail de produits de technologie avancée dont le concept modulaire permet de visualiser des améliorations pour l’avenir qui s’intégreront parfaitement à l’installation existante.
Un service après-ventes zéro défaut
Chaque projet de traitement de matériaux de CDE bénéficie de la méthodologie ‘Client à vie’ propre à la société. Elle consiste en un service avant, pendant et après-ventes suivi, favorisant un minimum d’intermédiaires, pour assurer une communication transparente et efficace dès le début du projet jusqu’à la fin de l’utilisation de l’installation.
M. Sebri conclut: «Nous sommes très satisfaits du rapport qualité-prix de nos équipements CDE. Nous apprécions particulièrement le service que nous avons reçu. Dès le début du projet, nous avons visité les usines de CDE en Irlande du Nord et avons été convaincus par la qualité des matériaux utilisés et l’expertise des ingénieurs tant au niveau de la conception que de la fabrication de notre installation.
CDE propose un service complet, de la conception au service après-ventes en passant par la gestion de toutes les étapes du projet, ainsi qu’un seul point de contact pendant la durée du processus, le tout basé sur 25 ans d’expérience internationale. Ceci est une proposition rassurante, surtout au vu des investissements requis et des enjeux de longévité de nos opérations.
M. Idriss, notre représentant CDE en Tunisie, ainsi que les ingénieurs de CDE sur site, ont été présents et à l’écoute à toutes les étapes du projet pour une réalisation sans accroc. Je peux dire sans hésitation que CDE a révolutionné nos opérations.