Sand, after water, is our most used natural resource. We are living through a global sand crisis, whereby the consumption of sand, for use in everything from construction to computers, has seen demand outstrip supply putting increased pressure on natural resources. It’s a finite resource that is rapidly depleting. It is estimated we use 50 billion tonnes of sand each year, and this figure is expected to continue rising.
It is fundamental to maximise sand recovery from existing supplies and use natural sands only when necessary to ensure we manage the world’s resources sustainably.
Around the world, millions of tonnes of sand are destined for use in lower value concrete due to naturally occurring contaminants such as lignite.
In this issue of our Innovation Series, Darren Eastwood, Business Development Director and John Quigg, Senior Technical Engineer, look at how our engineers have adapted contaminate removal technology to reach previously unattainable levels of lignite removal, maximising the value of the sand for use in higher value outputs.
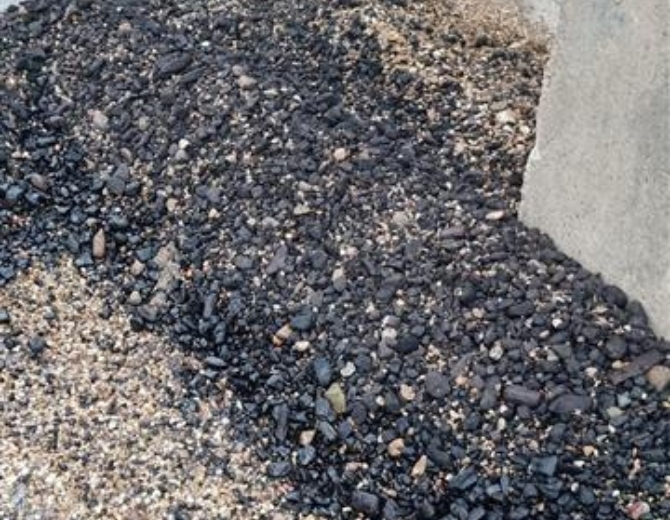
Empecemos por el problema.
El lignito es una sustancia blanda, negra o marrón, parecida al carbón, que puede estar presente en depósitos localizados de arena y áridos de todo el mundo. Se lo considera un contaminante en las industrias de la arena y los áridos, y puede tener 2 efectos perjudiciales si se integra en la producción de hormigón:
1. Tinción
Al terminar el hormigón, la fracción de lignito más ligera y blanda sube a la superficie y, a medida que el hormigón se endurece, el lignito se hace visible en forma de manchas oscuras. La gravedad de esta situación depende de la cantidad de lignito presente en el material. El impacto está determinado por su visibilidad en el hormigón acabado. El efecto perjudicial va desde pequeñas manchas hasta una decoloración importante.
Si las manchas se producen en hormigón que no es visible, como los cimientos, entonces no es un problema grave. Sin embargo, estas manchas no son deseables en un muro de hormigón visible, en una infraestructura importante o en productos como pavimento. No queda bien ni inspira confianza en la estructura.
2. Estallido
Si bien las manchas son antiestéticas, los “estallidos” son aún más problemáticos. El estallido se produce cuando el lignito más ligero sube a la parte superior de las losas fratasadas y los acabados arquitectónicos. Las partículas de lignito se expanden y explotan fuera del hormigón. Esto deja agujeros que pueden variar de tamaño. Puede tener un efecto perjudicial en la integridad del hormigón, dejar un acabado desigual, afectar a su desgaste y provocar problemas con los acabados. Una vez más, no inspira confianza en la estructura.
Por ello, las normas internacionales sobre los límites aceptables de contenido de lignito en la arena y los áridos para la producción de hormigón son muy estrictas y los depósitos contaminados se rechazan.
Dependiendo del uso final del hormigón, el nivel admisible de lignito en la arena puede variar. En EE. UU. y en algunos otros países como Tailandia se sigue la especificación ASTM C33 para el hormigón. Esta norma permite un 0,5 % de lignito en la arena si la superficie de hormigón es grande. Para el resto del hormigón, el contenido máximo permitido es del 1 %.
En el Reino Unido y en Europa, la norma EN 12620 permite un 0,5 % de lignito en la arena. Sin embargo, si la superficie de hormigón es grande, el límite de lignito disminuye al 0,25 %.
Algunos productores solo aceptan que su depósito tiene lignito y lo utilizan tal cual o lo venden para uso en productos de menor valor, mientras que otros buscan soluciones para eliminarlo.
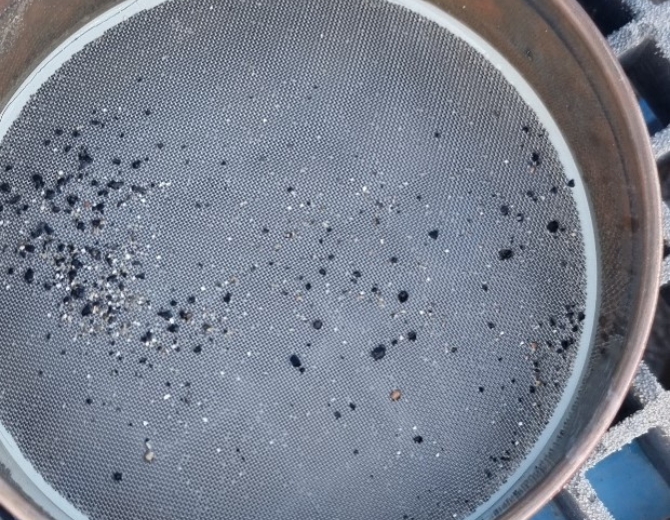
La solución tradicional
Para eliminar el lignito de la arena y de los áridos, los operadores solían usar tornillos.
Basados en la tecnología de los tornillos de agua, que existe desde hace milenios, los tornillos funcionan al agitar la arena en el agua para hacer flotar los contaminantes orgánicos o ligeros sobre un dique. Utiliza un flujo ascendente para generar una separación por densidad; el material más ligero flota y el más pesado se hunde. Como el lignito es más ligero que la fracción de arena, debería flotar. Las fracciones de arena más pesadas se hunden en el fondo del sumidero y se extraen para su posterior procesamiento mediante el tornillo giratorio.
El problema de esta solución es que los puntos de corte son imprecisos, lo que dificulta la producción sistemática de la arena que cumple con las especificaciones. Si bien la mayor parte de la fracción de lignito flotará, no toda lo hará. Normalmente, se requiere fricción para separar la arena del lignito. El movimiento del material por sí solo no puede producir suficiente impacto para lograrlo. Las pasadas múltiples por el tornillo pueden ayudar, pero esto solo mejora marginalmente el resultado, a la vez que agrega más tiempo al proceso y aumenta los costos.
En los últimos años, a medida que los productores de arena y áridos asumieron el rol que pueden desempeñar en la producción sostenible, observamos un aumento de las solicitudes para eliminar el lignito y otros contaminantes con el fin de mejorar la calidad del material y maximizar el rendimiento comercial. Los clientes están adoptando la producción sostenible porque entienden que no hay otra alternativa.
Elevar los estándares: el desafío del 0,1 %.
Hace poco completamos un proyecto con un productor de hormigón de EE. UU. que tiene grandes cantidades de lignito esparcido en su depósito de arena y áridos. En sus operaciones anteriores, utilizaba el método de tornillo y no cumplía continuamente la especificación C33.
Este cliente quería subir los estándares de calidad en la producción de arena. Ya no se conformaba con utilizar su valioso yacimiento para productos de menor valor, sino que quería abastecer a una base de clientes más amplia que exigiera productos de mayor calidad.
En lugar de limitarse a cumplir los requisitos de la especificación C33 del 1 % de lignito, nos desafió a diseñar una solución que garantizara el 0,1 %. Esto es 10 veces menos de lo que permite la especificación C33, pero le permitiría obtener un producto de mayor calidad y consistencia que podría vender en nuevos mercados a precios más altos.
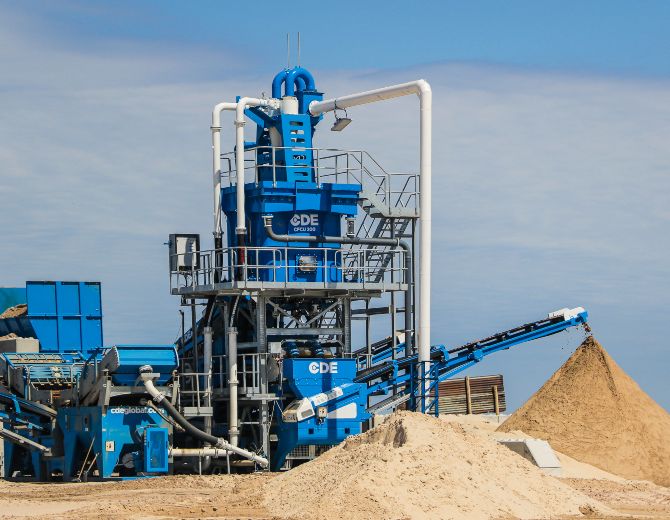-La-Chola-plant-overview-670x520.jpg)
Este desafío constaba de tres partes.
1. Eliminar el lignito de la fracción de arena para superar la especificación C33: objetivo del 0,1 %.
2. Clasificar la arena de una alimentación muy inconsistente para cumplir la especificación de tamaño C33.
3. Eliminar el lignito de los áridos para permitir su uso en el hormigón.
Durante la fase de diseño de este proyecto, colaboramos estrechamente con el cliente para analizar su material y los datos que había acumulado de sus operaciones anteriores. Realizamos pruebas de laboratorio y numerosas visitas in situ para conocer las capacidades de nuestros equipos y asegurarnos de que podíamos alcanzar los niveles que el cliente necesitaba. Utilizamos nuestra experiencia y los datos de otros proyectos de extracción de lignito para determinar el método más productivo y eficaz a fin de alcanzar los objetivos del cliente.
Un enfoque diferente
1. Extracción de lignito
We deploy a number of different plant items within our range to wash and classify material and typically use our Counter Flow Classification Unit (CFCU) for contaminant removal. The CFCU separates material based on density, and sizes material, in one process.
The CFCU uses counter flow forces, (also known as upward flow) in a chamber to classify material by gravity. Water is used to suspend sand particles and the high density in the chamber provides a boundary through which the lignite cannot pass. The density of the fluidised sand bed can be controlled at a set cut point allowing the heavier sand fractions to sink through this bed to the bottom of the chamber, while the lighter lignite floats out the top, giving us a controlled density separation.
We knew we could remove most of the lignite with the CFCU while retaining the fine sand, resulting in a higher sand yield. The challenge for us in this case is to set and maintain this specific density to maximise the removal and reach this ambitious target.
2. Extracción de arena
Para lavar y clasificar el material, utilizamos una serie de elementos de planta diferentes dentro de nuestra gama y normalmente utilizamos nuestra unidad de clasificación de contraflujo (CFCU, por sus siglas en inglés) para eliminar elementos contaminantes. La CFCU separa el material en función de su densidad y lo clasifica en un solo proceso.
Además, utiliza fuerzas de contracorriente (también conocidas como flujo ascendente) en una cámara para clasificar el material por gravedad. El agua se utiliza para suspender las partículas de arena y la alta densidad de la cámara proporciona un límite que el lignito no puede pasar. La densidad del lecho de arena fluidizada se puede controlar en un punto de corte establecido, lo que permite que las fracciones de arena más pesadas se hundan a través de este lecho hasta el fondo de la cámara, mientras que el lignito más ligero flota a la parte superior, lo que nos proporciona una separación por densidad controlada. Sabíamos que podíamos eliminar la mayor parte del lignito con la CFCU y conservar la arena fina, y así lograr un mayor rendimiento de arena. Nuestro desafío en este caso es establecer y mantener la densidad específica para maximizar la extracción y alcanzar este ambicioso objetivo.
3. Áridos
El tercer aspecto de este desafío era eliminar la contaminación por lignito del árido para que el cliente pudiera utilizarlo también en la producción de hormigón.
Nuestro lavador de piedras RotoMax™ se suele utilizar para realizar el fregado necesario y así eliminar la arcilla y los contaminantes de los áridos. Los ejes sincronizados con paletas de fregado en espiral mueven los áridos fluidizados a través de un sumidero inclinado, que friega el material y extrae los contaminantes.
A medida que la agitación libera el material, el flujo ascendente permite extraer el lignito más ligero de forma controlada. Como resultado de las pruebas de material, nuestros ingenieros determinaron que era necesario un flujo ascendente adicional y diseñaron una solución para aumentar el volumen y la profundidad del agua en el tanque. De este modo, se prolongó el tiempo de retención en el agua y se aumentó la eficacia de la separación por densidad dentro del lavador de piedras para maximizar la extracción de lignito y alcanzar los objetivos del cliente.
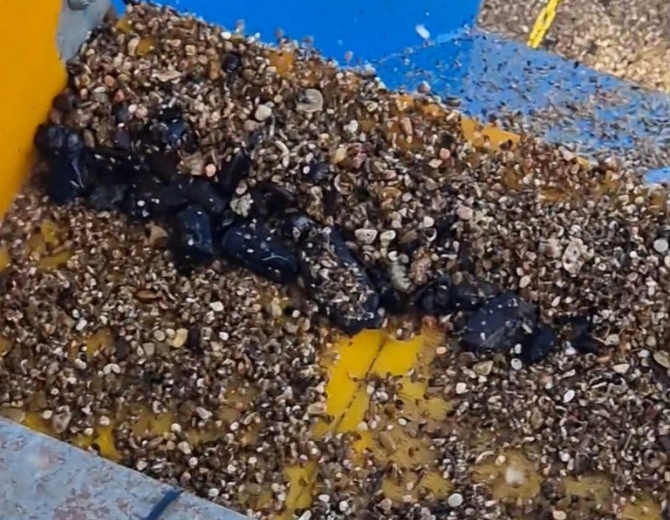
El resultado
Según nuestras pruebas de materiales y los datos de instalaciones anteriores, la CFCU se instaló y configuró a partir de unas especificaciones muy precisas. Cuando se obtuvieron los resultados de las pruebas del primer material, fue necesario realizar algunos ajustes menores para optimizar el rendimiento conforme a la especificación C33.
El producto acabado de arena se deslimó a un nivel superior al previsto por el cliente y alcanzó una equivalencia de arena de 99, muy por encima de la especificación ASTM de 85.
En el caso de los áridos, el éxito inmediato del sistema fue evidente, ya que el lignito y el carbón de 5 cm-10 cm/2 in-4 in se eliminaron eficazmente con una pérdida mínima de producto. La solución con RotoMax produjo un árido limpio listo para su uso en la producción de hormigón.
Beneficios adicionales
Si bien el objetivo era mejorar la calidad del producto para el cliente, se obtuvieron otros beneficios que mejoraron la sostenibilidad del proyecto a largo plazo. Este nuevo sistema puede procesar mayores volúmenes de material que el antiguo tornillo, por lo que la capacidad de producción aumentó drásticamente y se mejoró la eficiencia. Al eliminar la repetición del fregado y la doble manipulación, se redujeron los costos de mano de obra. Esta solución más robusta permite a la planta trabajar a doble turno con un tiempo mínimo de inactividad por mantenimiento.
Nuestro objetivo es maximizar la recuperación de cada grano de arena, lo que permite a los clientes aprovechar todo el potencial comercial de sus materiales. Mediante la extracción de lignito y otros contaminantes, podemos mejorar la calidad de la arena, minimizar los residuos y prolongar la vida útil de las operaciones marginales. A su vez, esto reduce el impacto sobre los materiales vírgenes.