The first ProPress high-performance filter press to be commissioned by wet processing experts CDE has exceeded processing targets and significantly reduced reliance on costly settling ponds, says the owner of one of Scotland’s leading aggregate specialists.
Developed to meet the evolving needs of the construction and demolition waste recycling, quarrying, and mining sectors, the ProPress integrates the latest technological advancements to deliver exceptional operational efficiency and maximum water recovery.
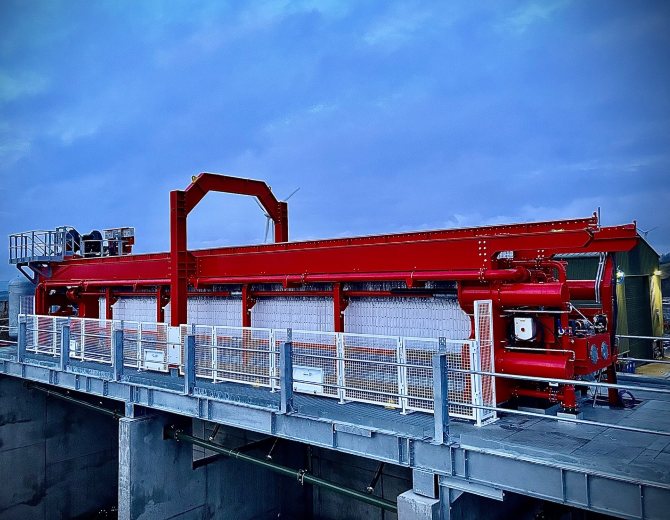
ProPress Pioneers
Collier Quarrying and Recycling Ltd. was the first CDE customer to integrate the new ProPress filter press into its wash plant setup. Commissioned in April this year at the company’s Goathill Quarry in Fife, its ProPress X4-200, the largest model in the new range of filter press, benefits from 200 plates and can process 20m3 per mechanical cycle.
A longstanding customer, Collier Quarrying and Recycling Ltd. operates two existing CDE wash plants.
“I have two CDE plants and they’re really good plants,” said owner Duncan Collier. “They’re very efficient, so when I found out CDE was designing its new filter press I knew it wouldn’t let me down. We’re very familiar with the technology under the hood and fully trusted CDE to deliver – and they really have.”
By the end of 2024, the new CDE ProPress will be found on eight wash plants across three regions, processing around 1000tph of material.
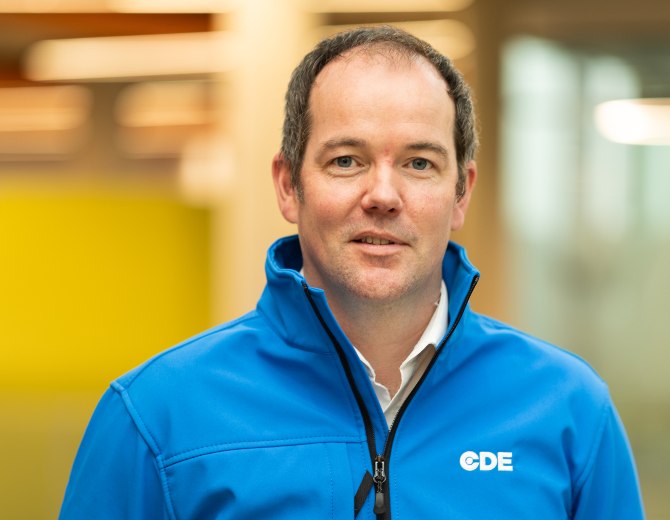
The Problem With Ponds
With the CDE ProPress, owners and operators can recycle up to 95% of process water for immediate reuse in their wash plant, eliminating the need for settling ponds which typically require extensive maintenance, consume labour resources, and incur significant costs.
CDE business development manager Fergal Campbell said: “Settling ponds are known to be a source of considerable revenue losses. They occupy a very large site footprint, maintenance costs are high, and they adversely impact the production of saleable material due to the amount of management needed. With the CDE ProPress, we can address many of these pain points with a single solution.”
When Collier Quarrying and Recycling Ltd. acquired Goathill Quarry it began recycling demolition waste into reusable aggregates and sub-base materials, a process that requires significant water resources along with its virgin material processing.
“We’ve been managing settling ponds for over a decade now. More and more, our business is focused on recycling demolition waste and as that side of the business continues to grow our water needs increase substantially,” Duncan said.
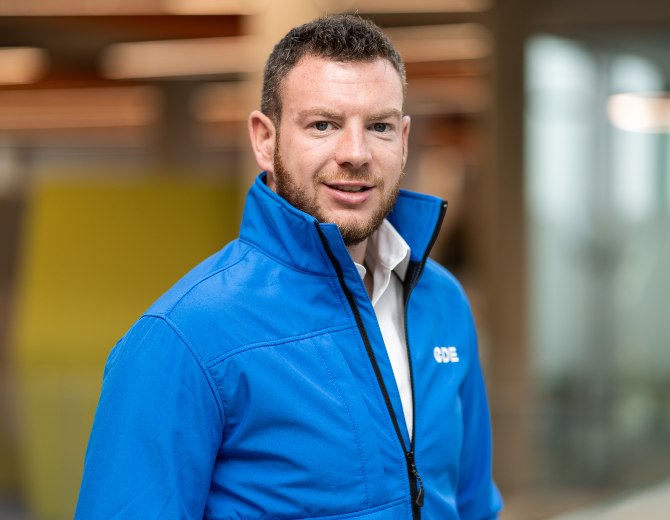
Jordan McCooe, CDE Programme Manager UK & Ireland, said: “For Collier, the challenge with pond management was doubled because it required clean water to supply two active wash plants. Initially, it was thought that two filter presses would be needed; one for each plant. When we reviewed current and projected throughput, we found that a single, large filter press had the capacity to process materials from both plants.”
The CDE ProPress is available in eight different sizes to suit all markets and applications, ranging from the ProPress X1-60, which has 60 plates and can process 6m3 per mechanical cycle, to the ProPress X4-200, which has 200 plates and can process 20m3 per mechanical cycle. A centrally located 600m3 buffer tank is receiving sludge from both wash plants simultaneously.
Jordan continued: “The ProPress features plates that are 25% larger. The combination of greater chamber volume, fewer plates overall, and the buffer tank means that just one ProPress unit had the capacity to receive and process sludge from both of Collier’s wash plants.”
It has allowed Collier Quarrying and Recycling Ltd. to reduce its reliance on settling ponds, Duncan said. “This is hugely positive, not only from a production standpoint but also in terms of health and safety. There’s less maintenance involved and open water areas have been scaled back greatly.”
With the CDE ProPress, safe and efficient maintenance is made possible by integrated plate-shaking technology which addresses filter cake build-up within chambers to help reduce the need for manual intervention. An access walkway provides clear and unobstructed means to carry out maintenance safely and efficiently, and flush mounted drip trays reduce material entrapment and lock in place to provide a secure maintenance platform for operators.
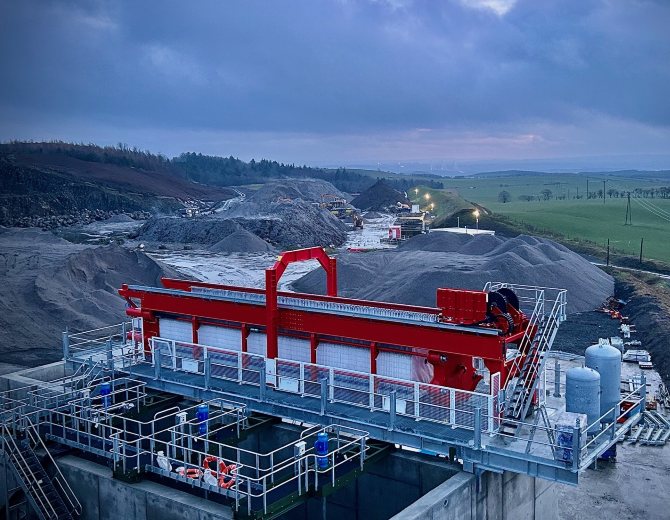
Engineered For Profitability
Operational now for three months, the new ProPress is processing at a higher volume than anticipated,” Duncan said.
“It’s capable of doing what CDE said it would do, and more besides. It’s absolutely first class and helping to really accelerate our return on investment.” Commenting on the functionality of the CDE ProPress, Duncan said it’s “very user-friendly.”
The smart design of the CDE ProPress is supported by an innovative, multifunctional robot, which serves as the main workhorse for the ProPress, controlling plate opening, plate shaking, cloth washing, plate winch, and the maintenance platform.
Once the ProPress is commissioned, every customer is also introduced to the CDE CustomCare team which provides aftersales support to help achieve maximum performance from their equipment. On any given day, the UK and Ireland team has eight service vans and six pick-ups on the road supporting customers to meet their production targets.
The CDE ProPress is available in a range of different sizes to suit all markets and applications. Available globally, the ProPress is also largely pre-assembled to minimise construction time on site and expedite commissioning, allowing operators to get up and running quickly to help achieve fast return on investment.