CDE commissions silica sand plant in Scotland to meet growing market demands
Fife Silica Sands sought to expand its operation and maximise yield of its products
With high quality silica sand resources scarce globally, Fife Silica Sands has partnered with CDE to commission a 210 tonnes per hour (tph) silica glass sand plant to meet the growing demands of the market.
Fife Silica Sands, located at Burrowine Moor Quarry in the central lowlands of Scotland, is owned and operated by Paterson Quarries.
Founded over fifty years ago, Paterson Quarries operates eight sites through Scotland, supplying a range of materials including concrete, specialist sand and recycled aggregates across the UK. Now a third-generation family firm, Paterson Quarries acquired Fife Silica Sands in 2002.
Passionate about delivering high quality across all of its operations, Paterson Quarries has provided sand to prestigious golf resorts across the UK and Ireland, including Loch Lomond and Ardare Manor, as well as for professional football and rugby facilities.
CDE, a leading provider of wet processing solutions for the natural and waste recycling sectors, has been working with Paterson Quarries for over fifteen years. The two firms first partnered in 2011 on a modular sand washing plant.
Having developed a strong working relationship together, the team at Paterson Quarries knew that CDE would be the right partner to work with Fife Silica Sands in order to meet market demands.
Showcasing its capabilities in providing solutions for silica sand, CDE welcomed Fife Silica Sands to its manufacturing facility in Northern Ireland, as well as taking the team to reference sites across the UK, so that the team could see the technology in action.
Commenting on the decision to partner with CDE again, Tom Paterson, Managing Director of Paterson Quarries said: “From previous projects and years of experience working together, we knew that CDE would be the right choice. Our ultimate goal was to deliver a top-quality silica sand to customers across the UK and Ireland. CDE’s team meticulously tested material in their lab to get a true understanding of our expectations and the materials we wanted to produce, so that they could design the right plant for us.”
Chris McKeown, Director of Customer Solutions at CDE added: “Throughout all the projects we've delivered for Paterson Quarries the customer's input has been critical within this process, and we try to incorporate all the requests into the design of the plant. This included visiting multiple reference sites, testing of the material in our lab, flying over for inward visits with our design team in-house.”
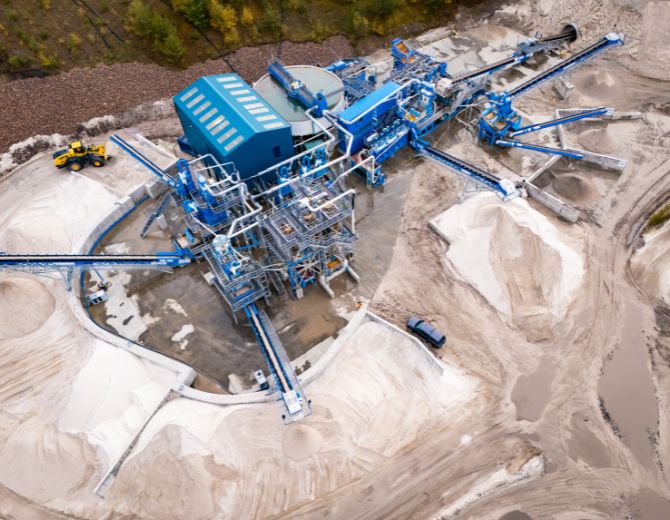
Consistency at its core
The glass industry is the largest end-user of silica sand production at more than a third of the total market globally, followed by foundry, hydraulic fracturing, filtration, and abrasives.
The construction market, rising automotive production, and technological advancements such as increasing usage of hybrid guide plate for use in computer monitors, smart phones, and televisions, solar control glazing for automotive and building glasses, lightweight glazing glass, and advanced nanotechnology in flat glass are all increasing demand for high-grade silica.
With silica sands, a critical aspect is consistency. In order to deliver products that were dependable and meet market specifications, CDE designed and engineered a 210tph sand washing solution which was commissioned in February 2024.
The solution comprises of three EvoWash™ sand washing systems, one for amber sand, one for glass sand and the third for fine sand, two five Infinity™ fine sand screens, AquaCycle™ high-rate thickener and an AquaStore water storage and recirculation system.
The three EvoWash systems contain modular hydro cyclone technology to allow for unparalleled control of silt cut points, ensuring that Fife Silica Sands can provide consistent, in-spec product to meet the needs of the market.
CDE added two five Infinity fine sand screens which ensure the even distribution of power material across the full screening area for superior screening and dewatering performance.
The AquaCycle is a highly efficient water management solution that minimises costly water consumption and is allowing Fife Silica Sands to recover 80% of the process water to be recycled for immediate recirculation.
The AquaStore receives recycled water from the AquaCycle which is then recirculated, reducing the volume of fresh water required to feed the washing plant.
Tom Paterson added: “From an environmental point of view, this plant is a real win for us, as there is less waste and we’re recovering more. We have a direct wire to a wind turbine, so we have all the needs for this plant from renewable energy when the wind blows.”
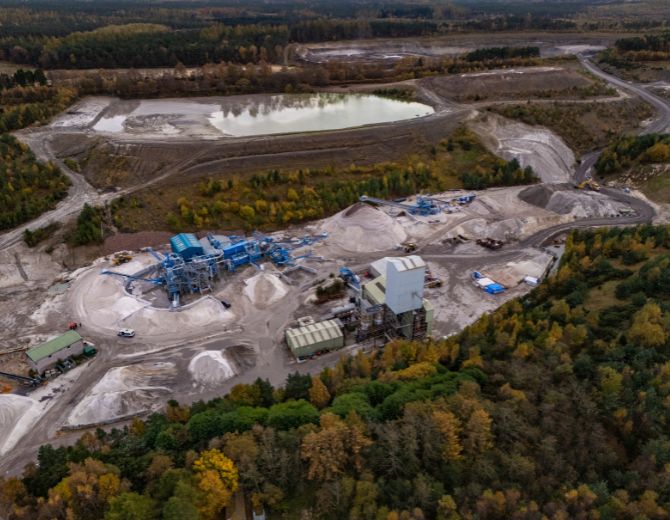
Around the clock performance
Fife Silica Sands’ wash plant is operating 24 hours a day, 7 days a weekMonday to Friday, in order to keep up with supply needs of the industry. With an around the clock operation, CDE installed its SmartTech plant management app, which enables Fife Silica Sands to understand its plants performance, schedule maintenance and easily order parts.
Sensors fitted to a plant provide up to 300 precise data points and continuously stream real-time, in-depth performance reports. Providing a full and transparent overview of the health of a plant, this live feed is accessible 24/7 through a handy mobile app.
With this technology, Fife Silica Sands can watch input feed rates, the hopper speed, thickener and water tank levels remotely.
“With CDE SmartTech, we can track the performance, we can see the settings, and we can look back and view what changes have been made through the plant and how it has affected the quality or yield of the end product. Whilst this is a complex plant, SmartTech allows us to easily analyse the overall performance of the plant,” says Mr Paterson.
Kenny Mitchell, Quarry Manager at Fife Silica Sands adds: “From install, right through commissioning and into after care, CDE has always been very forefront and helpful with enquiries. If we need any products, or spare parts, or any issues that we've had, we've been able to raise them with the customcare team and they have been able to resolve either remotely with the aid of SmartTech or by having engineers visit sit
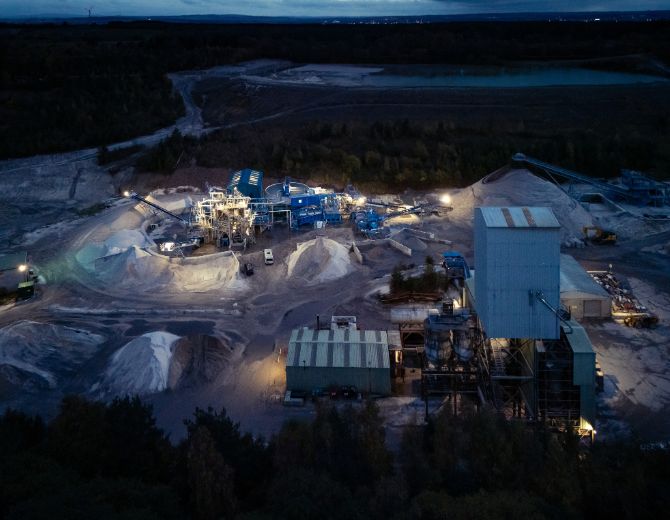
High quality product creating long-standing partnerships
With this sand washing solution, Fife Silica Sands is able to produce seven products to supply the market. The two glass sand products are the main outputs from the plant and there are a number of other fractions used for a range of applications from sports sands through to construction aggregates.
Chris McKeown says that consistency is key with glass sand production.
“The output products from Fife Silica Sands will go into numerous applications in the glass industry. Product quality is key, and we were determined to provide a solution that could deliver consistent, high-quality products. And that's what we're able to track and deliver with the plant.”
Delighted to see the plant exceeding expectations, Tom Paterson says: “We’re supplying thousands of tonnes of specialist sand weekly to large glass manufacturers across the UK, who are producing the highest quality glass, as well as sand suitable for cattle bedding, horse riding arenas and play parks.
“This is a new and different approach for us, and we’re getting a much higher yield from every tonne of product, and far in excess of our expectations. We have one glass customer who has signed up to work with us for twenty years, which is a testament to the quality of the products we’re supplying.
“At Paterson Quarries, we pride ourselves in what we do, and we live by our ethos in providing quality products at competitive prices, combined with delivering reliable service and friendly, knowledgeable staff, and CDE’s technology has allowed us to continue this with our latest investment. ”
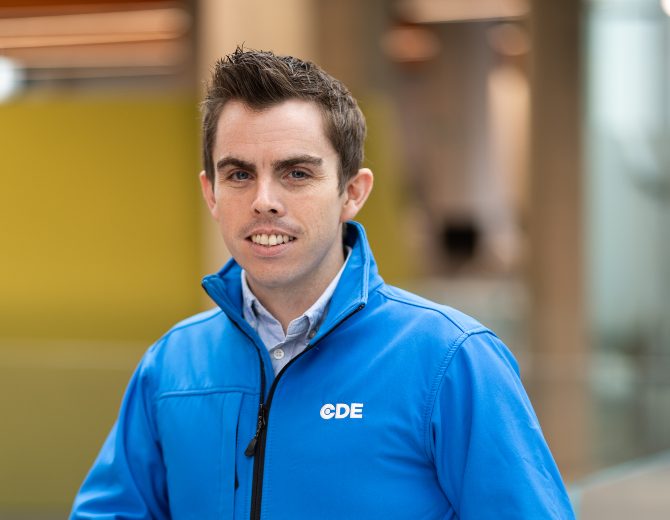
Chris McKeown concludes: “This is a project I've been involved with right from the early sales stage, through the engineering process, the installation, and now into the fully operational phase. It's great to see the plant now at this stage.
“Across our industry tonnes per hour is a common metric used to describe the performance of a plant. But ultimately, the return on investment of a plant like this is built on achieving that tonnage over an extended period of time. So, in CDE, the key metrics for us are tonnes per week, tonnes per month, tonnes per year, over many years.”
CDE and Fife Silica Sands will be hosting a virtual tour on 26th March to showcase this 210tph solution, and how it is allowing the business to meet the growing market demands.
For more information, or to register for this insightful virtual tour please register below.