Tonnage
50tph
Material
Road Sweepings & Gully Waste
Output
1 Sands | 2 Aggregates
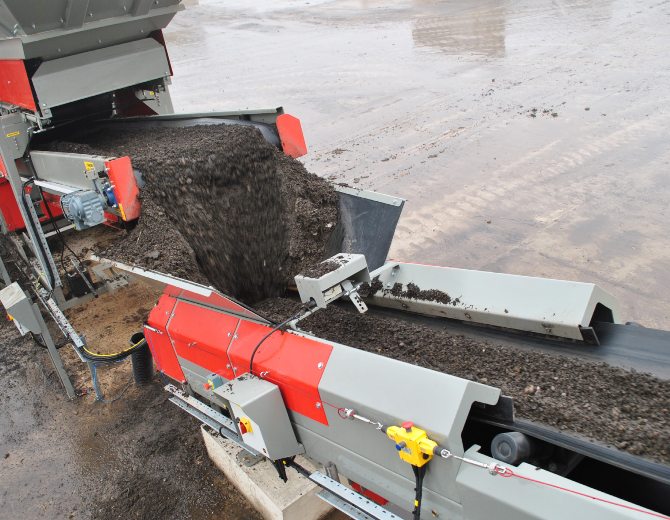
THE CHALLENGE
Veolia Environmental Services is the leading recycling and waste management company in the UK providing commercial, industrial and local authority customers with sustainable recycling and waste services, turning waste into a resource.
Veolia has a number of contracts with city councils and waste authorities (Birmingham City Council, Shropshire Council, Nottinghamshire County Council) which generate a significant volume of street sweepings every year. The previous process used by Veolia saw 100% of this material go to landfill at great cost environmentally and economically.
The company is situated on a working landfill site and therefore has an on-going need for restoration material. This site has specific restoration criteria which the processed material must meet to be suitable for landfill restoration.
The system was required to divert 85% of street sweepings and gully waste from landfill and send less than 15% residue to landfill. Extensive performance tests were conducted by Veolia to confirm the suitability of the CDE application and ensure the quality and reliability of the outputs.
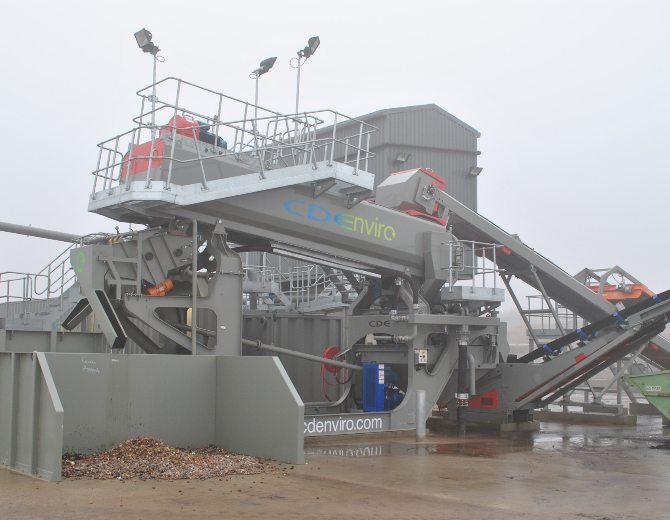
THE SOLUTION
Extensive research was carried out into the technologies available for recycling road sweepings and gully waste which led Veolia to recognise CDE as specialists in this area. The project brief for CDE was to develop a washing treatment process for road sweepings and gully waste to produce landfill restoration materials and recyclable aggregates for on-site capital schemes.
The CDE recycling system is a semi-automatic plant which processes 50tph of road sweepings. The system accepts road sweepings and gully waste, most of which is dewatered off site to allow bulk transportation by truck to the Ling Hall recycling facility. Wet waste can also be accepted and processed and the water is pumped to the plant for treatment.
The material is fed into the AggMax ™ logwasher and aggregates are scrubbed to break up clays and remove contamination from the stone. Lightweights and organic material are discharged onto the dewatering screen to remove excess water while the aggregate is screened into two washed products and sand is removed.
Sand and process water are pumped to the EvoWash™ fine materials classification system and the material enters the sump of the EvoWash and is pumped to the hydrocyclone where wastewater and silt are separated from the sand and the dewatered sand product (12-15% moisture content) is discharged to the stockpile conveyor.
The decanter centrifuge is used to separate the fine solid material from the water, removing hydrocarbons and reducing heavy metals. Clean water is then stored in the AquaStore for recirculation around the system and 50% dry solids are discharged into a stockpile.
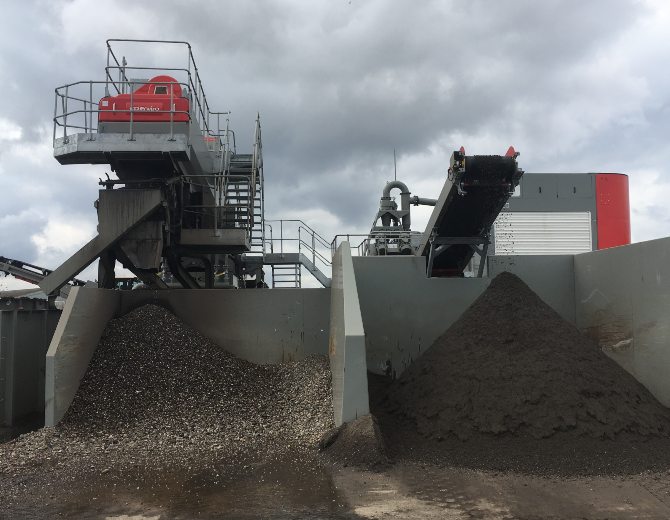
THE RESULTS
Processed outputs include +20mm aggregate, 20-5mm aggregate and -5mm sand. Oversize material such as rags, twigs and large stones are processed via the trommel screen leaving the ferrous metals, organics and plastics to be sent for recycling. The decanter filter cake is then used for landfill remediation with the aggregates and sand used for onsite construction. This also reduces the need to purchase virgin aggregates.