Tonnage
100tph
Material
Sand & Gravel
Output
Washed sand, 6-8mm & 8-12mm aggregates
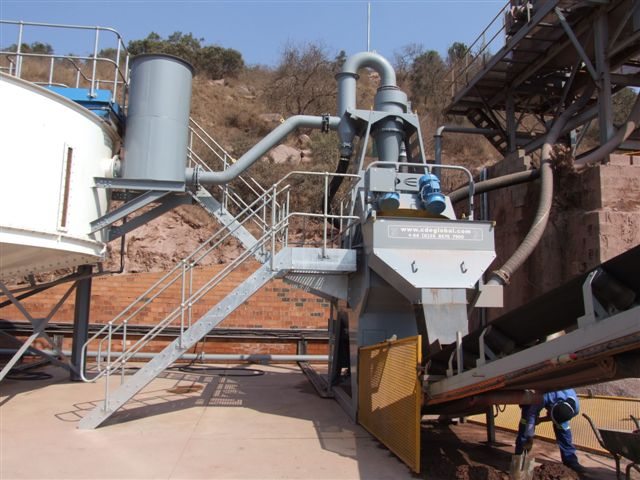
THE CHALLENGE
NPC is a subsidiary of global construction materials producer, Cimpor of Portugal and operate eleven facilities in South Africa with total production of 1.7 million tonnes. These include seven ready mix concrete plants, three aggregate production plants of which Sterkspuit is one, two grinding plants and one cement plant. Sterkspuit quarry is located in the Cliffdale area some 30km from Durban on the eastern coast of South Africa.
Prior to the introduction of a new washing plant, it was the sand washing process which was the biggest area of concern for Natal Portland Cement. Due to inefficiencies of the old plant, the company had to buy up to 80 per cent of the fine sand used for downstream production. This led to significantly increased production costs.
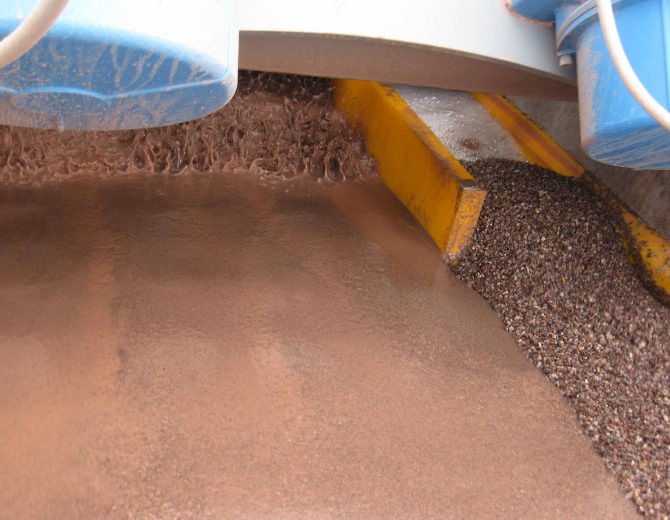
THE SOLUTION
From the crushing plant the minus 9.5mm material is first sent to a CDE Prograde P2-75 double deck rinsing screen fitted with modular Isenmann polyurethane panels on both decks. The Prograde produces a 6.7-9.5mm and a 5-6.7mm aggregate with the minus 5mm material being delivered to the sand washing phase. The CDE Evowash™ 71 washing plant introduced to replace the bucket wheel de-waterer previously employed eliminated the loss of quality fines in the sand processing phase.
The introduction of the AquaCycle™ high-rate thickener allowed for the recycling of 90% of the water used in the washing of their crushed material, while removing the need for settling ponds.
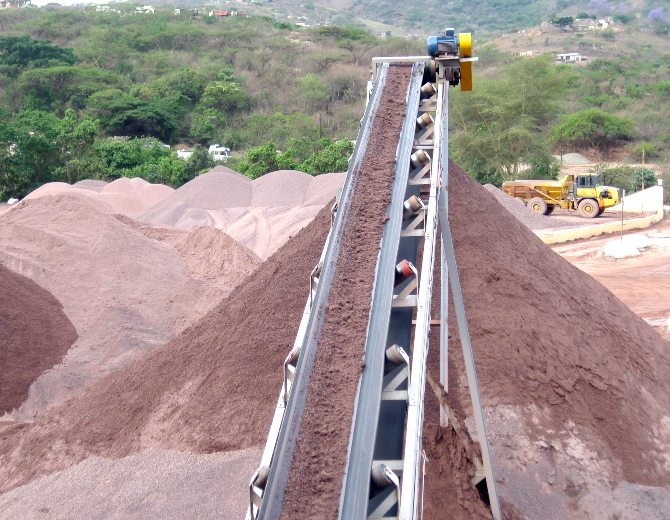
THE RESULTS
The advantages of polyurethane screen media on the screen have been immediately clear with enhanced performance in the first few months of operation and a reduction in the costs of maintenance. On the previous washing plant, the wire meshes had been lasting only a few weeks due to the abrasive nature of the material being processed. An additional advantage is the ease of fitting of the modules when compared with side tensioned wire meshes from a health and safety point of view. Production was considerably improved following the introduction of the EvoWash™ and the AquaCycle™ allowed for a better use of natural resources as well as optimal footprint on the site.