Tonnage
150tph
Material
Lignite Removal, Sand & Gravel
Output
0-5mm washed sand | 5-60mm washed aggregates | 60mm+ oversize
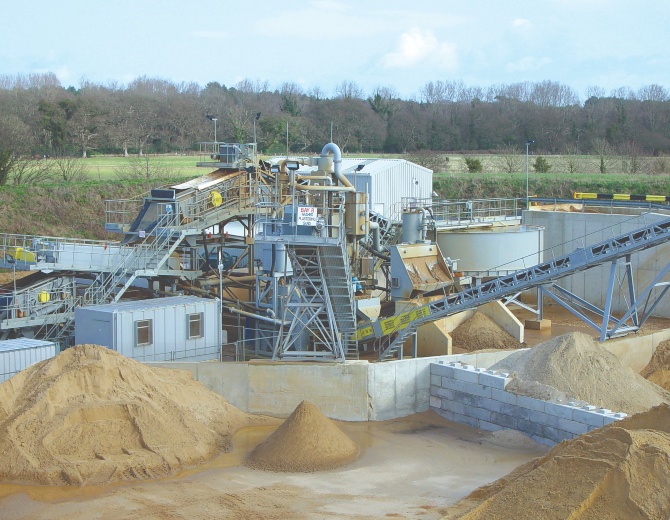
THE CHALLENGE
New Milton Sand & Ballast approached CDE for a sand washing solution to help address a lignite challenge they had within their feed material. Based in Hampshire, England, the team at New Milton needed to find a way to remove lignite from their sand, and in the process improve the quality of their sand and the efficiency of their wash plant. Using our co-creation approach, CDE’s team of technical engineers worked alongside New Milton to create and deliver a bespoke wet processing plant which removed the lignite and produced a range of in-spec sand and aggregates ready for the local construction market.
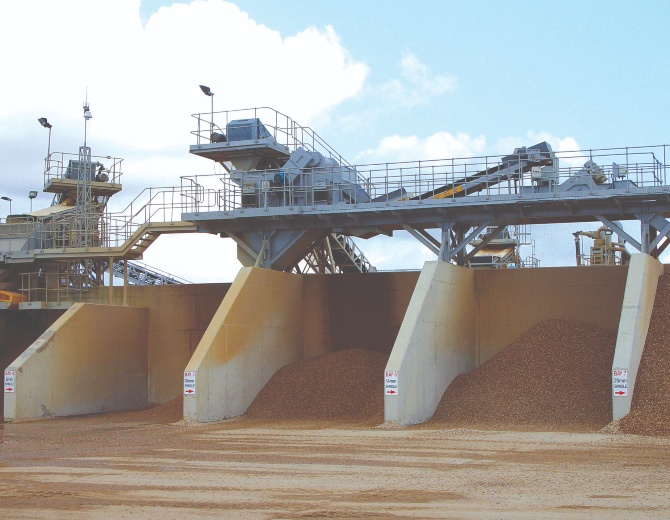
THE SOLUTION
The equipment supplied for this bespoke solution includes a feed hopper, a number of models from the CDE ProGrade screen range, a RotoMax log washer, the EvoWash sand wash plant, an AquaCycle Thickener, a crusher and a Belt press as well as several conveyors of various specifications.
At the outset, the raw material is fed into a 35-tonne feed hopper via dumper truck where material is then transferred to a 25m conveyor. CDE’s range of feed hoppers have been designed with efficiency in mind. This piece of equipment contains a variety of health and safety guards to minimise the risk of any on site accidents. While paying strict attention to this important issue, CDE have also focused on ensuring that maintenance time is kept to an absolute minimum. This has been achieved through the introduction of several design innovations.
“We have ensured that it is a one-man job to remove all the health and safety guards on our feed hoppers” explains CDE’s Design Manager, Brian McCullough. “This results in time saved during maintenance – the ultimate result of which is maximum production time.” In addition to this, all the maintenance points on the feed hopper can be easily accessed – again saving maintenance time. The localisation of all the grease points further reduces maintenance time, while also reducing the likelihood of operational problems as a result of gaps in the maintenance regime.
The next stage in the process involves the transfer of the feed material on to the first of CDE’s ProGrade screens – on this occasion it is a 5m x 1.8m double deck rinsing screen. The +60mm oversize, of which there is approximately 10 tph is rejected from the top deck to the oversize bay. The ProGrade screen range has again been developed with the aim of maximising performance and efficiency. One important way to ensure this is achieved is to ensure the maximum open area of the screen. This ensures the maximum tonnage on the screen while also increasing the dewatering capability of the screen.
As the process continues, the sand from the feed material (approximately 60tph) is washed through the bottom deck of this rinsing screen and piped to the EvoWash and the +5mm to -60mm material (80tph) passes over the bottom deck to the 82/7 Rotomax Logwasher. As with all of the equipment provided by CDE, the focus is on using high quality components to ensure maximum performance. The use of chrome molybdenum blades on the RotoMax logwasher effectively means that these blades are no longer a wear part.
“Our focus with all of our products is to use the highest quality components to ensure that the equipment performs to the highest possible level” explains Design Manager, Brian McCullough. “The result of this is higher efficiencies and production for the customer, which ultimately means higher profits.” The scrubbed material from the RotoMax logwasher is discharged out of the front of the log washer onto another ProGrade screen – this time it is a 3m x 1.5m double deck rinsing screen. The wastewater from the rear of the log washer is piped to the EvoWash sand wash plant. The discharge from the top deck of this rinsing screen (25tph) is conveyed to the crushing station while the remainder (50tph) passes over the bottom deck and is conveyed to the natural screening station. The remaining sand from the aggregate is washed through the bottom deck and fed to a ground sump. A vertical warman pump is used in the sump to pump the sand and water to the EvoWash plant.
The EvoWash sand wash plant processes approximately 70tph (60tph from 1st screen & 10tph from other screens) of lignite contaminated sand. This process uses a series of cyclones, upward flow classification tanks and sieve bends to produce three different products - a lignite free concrete sand, building sand and a waste lignite contaminated sand. One of the major issues with a lot of sand washing installations is the loss of fines to the ponds. The CDE EvoWash sand plant range tackles this problem through the use of hydrocyclone technology.

THE RESULTS
The EvoWash range offers the customer the opportunity to define the cut points for the sand to be produced. “Our EvoWash sand plants, in their various forms are proven to deliver customers the best possible results from their washing operations” explains David Kinloch, UK Business Development Director for CDE. “We can guarantee that only your -63 micron material is sent to the ponds, thus maximising the quantity of sand produced by the washing operation.” In addition to this, the dewatering capability of the EvoWash fine sands wash plant is industry leading. “We can offer our customers dewatered sand with a moisture content of around 12%” adds Kinloch. “In fact, in a large number of cases we have delivered sand with a moisture content of less than 10%.” The key to these results is the fact that each of the CDE EvoWash plants is customised to the specific output requirements and material characteristics of the individual customer.
“We understand that in no two operations, is the feed material likely to have exactly the same characteristics” explains David Kinloch. “Therefore, it does not make sense to offer an off-the-shelf product that makes no attempt to address the individual characteristics of both the feed material, and the customers output requirements.”