Volume
250tph
Material
Crushed Rock, Quarry By-Products, Limestone, Sand & Gravel
Output
Concrete sand | 40-50mm, 20-40mm, 14-20mm and 5-14mm aggregates
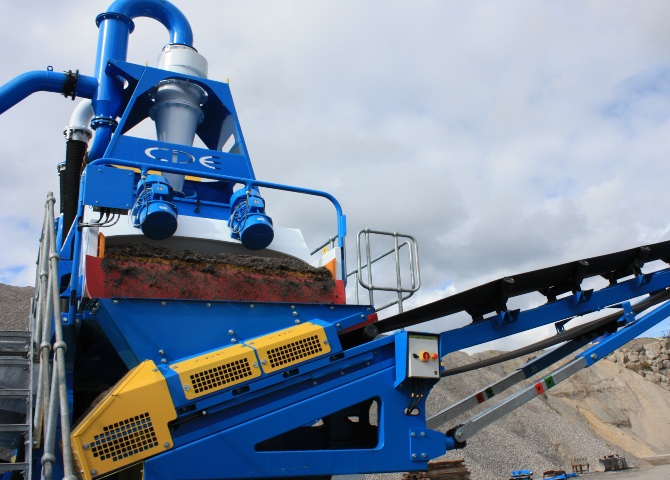
THE CHALLENGE
Gleeson Quarries was established in 1987 to serve the growing market for quality construction materials in Tipperary and surrounding areas. Its location at Laffansbridge, near Killenaule, allows for convenient access to the nearby major urban areas.
The company supplies a full range of readymix concrete, concrete blocks, crushed limestone, granular fill, agricultural lime and washed sand and gravel for the construction sector. Gleeson Quarries is one of the leading suppliers of Clause 804 and Clause 810 road materials to the local authorities for the many road building and improvement schemes that have taken place in the local area in recent years. Its main markets are within a twenty five mile radius of their Laffansbridge quarry.
Sister companies, Gleeson Concrete based in Tipperary town, produces readymix concrete, concrete blocks, sand and gravel, while Gleeson Precast based in Golden produces precast concrete floors. The Gleeson family has been involved in the construction materials market for almost 50 years and the second generation of the Gleeson family currently manages operations.
In operation since the late 80s, its traditional dry crushing and screening technology wasn’t able to extract maximum value when processing which resulted in a lot of waste material. The company wanted to find a way to improve efficiencies, reduce waste and maximise yields.
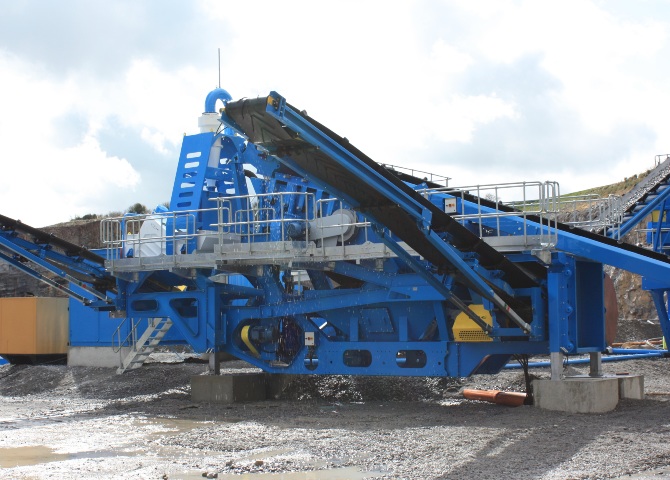
THE SOLUTION
CDE recommended a modular wash plant solution that included the M2500 mobile washing plant, AggMaxTM attrition system and AquaCycleTM thickener. The M2500 integrates a feed system with a ProGrade P2-75 double deck rinsing screen and EvoWashTM 71 sand washing system.
Material is fed to the hopper which removes the +100mm material. From the feed conveyor material is discharged to the ProGrade double deck rinsing screen – the top deck removes the +50mm material which is stockpiled using one of the 9m wing conveyors. These wing conveyors discharge at 4.7m offering a stockpile capacity of 150m3. The bottom deck removes the 5mm to 50mm material feeding it to the AggMax via the 9m wing conveyor, while the minus 5mm material is pumped to the integrated EvoWash system where the concrete sand is produced.
Due high levels of silts and clays, aggregates require additional attrition to get the cleanest products possible. This is achieved through the AggMax system with integrated Rotomax log washer and dewatering screen on a single chassis. The dewatering screen is fitted with spray bars to give the aggregates a final rinse. The 5mm to 50mm aggregates are then delivered to a 4 way split which classifies material into the desired grades.
An AquaCycle thickener system helps Gleeson’s recycle more than 80% of the water used in the washing plant. Waste water from the EvoWash is sent to the thickener via gravity feed and all of the minus 63 micron material enters the deaeration chamber on the thickener tank where the polyelectrolyte is added before the material is piped to the centre of the tank. A set of rakes at the bottom of the tank ensure that the settled sludge is maintained at an even consistency while the clean water overflows the weir and is set to the AquaStore pumping system for recirculation around the plant. An automatic sludge pumping mechanism is then employed to pump the sludge from the thickener to onsite settling ponds.
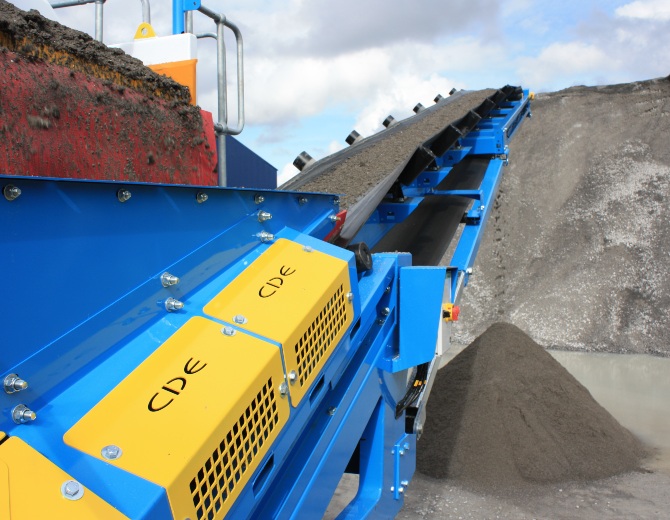
THE RESULTS
The M2500 has a total capacity of 250 tonnes per hour and produces 70 tonnes per hour of a single washed sand to the required specification. In this instance Gleeson Quarries required a concrete sand for use in its onsite concrete batching plant. There are a number of other models available within the M2500 range allowing up to 120 tons per hour of single or dual sand production if required. Meanwhile the integrated AggMax is producing four washed aggregates - 40-50mm, 20-40mm, 14-20mm and 5-14mm.
Within its first 5months of operation, the wash plant processed approximately 100,000 tonnes of material that was previously considered a waste product and was taking up valuable space onsite before installation of the washing plant. The customer realised a significant revenue opportunity through the introduction of an effective washing plant. The CDE sand and aggregate washing plant at Gleeson Quarries has addressed its operational issues and resulted in the customer being able to maximise returns from its extraction processes.
At a time when operators are focused more than ever on maximising efficiencies within their sand and aggregate processing operations, this project proves that there are significant opportunities to be taken advantage of with the processing of “waste” stockpiles.