Tonnage
300
Material
Crushed Rock, Quarry By-Products
Output
2 Sands: 0-2mm, 2-4mm and 4 aggregates: 4-8mm, 8-11mm, 11-16mm, 16-22mm
Feiring AS invests in a new crushing and washing plant to process quarry waste.
CDE and Norwegian partner, Nordic Bulk, recently supplied a second plant to Feiring AS to enable the recovery of up to 300tph of quarry dust material at its Bjønndalen quarry, helping the company to reduce waste and preserve natural resources in Norway while recovering valuable sand and aggregates that are in-demand in the construction industry.
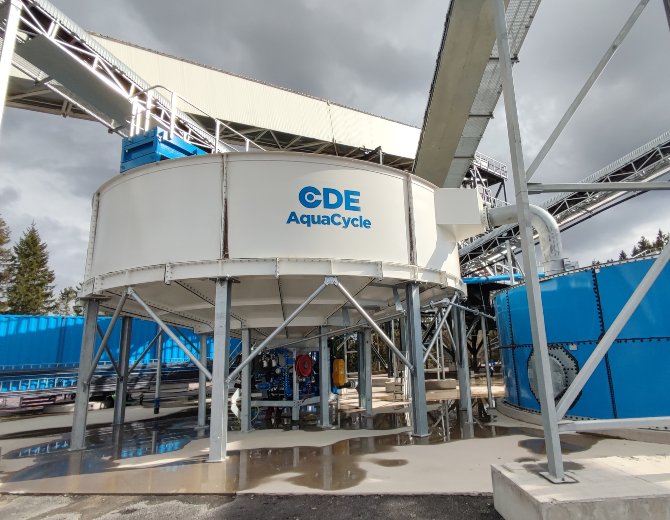
The Problem
Natural sand is the most consumed natural resource after water, and in some places this non-renewable resource is already in short supply. At the same time, crushed stone quarries face a recurring problem in that around 20% of their output consists of low value “waste” materials for which it is difficult to find a use.
Feiring was looking for a way to maximise the potential of its Bjønndalen quarry by utilising 100% of what is extracted and recover old residual masses from the crushing operations. Most importantly, the company needed to produce industrial (or manufactured) sand that has the same properties as natural sand to use in concrete production.
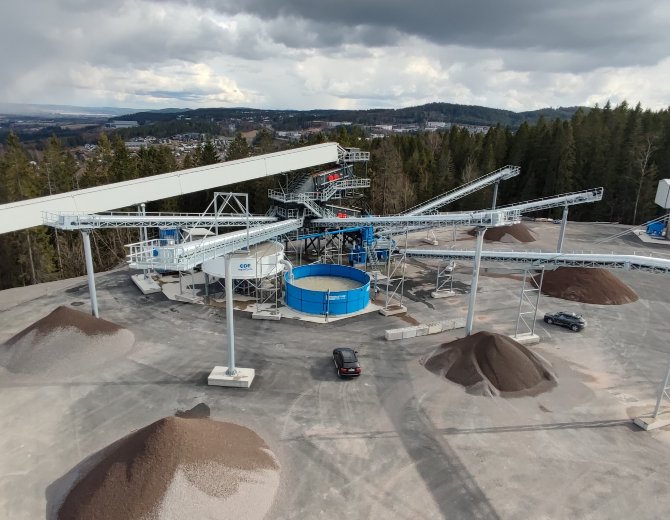
The Solution
Feiring invested in a new crushing and washing plant designed and supplied by CDE and their Norwegian partners, Nordic Bulk, to wash by-product materials from crushed stone production and produce high-quality industrial sand.
With a processing capacity of 300tph, the plant incorporates an EvoWash™ sand washing system and a full water management system, as well as two high-volume WIMA screens at the top. Thanks to its advanced hydrocyclone technology the EvoWash provides unparalleled control of silt cut points which guarantees in-spec sand straight from the belt. In addition, the combination of an AquaCycle™ thickener for primary stage water management and a filter press for sludge dewatering allows the for efficient water recovery and reuses up to 95% of the process water in the process.
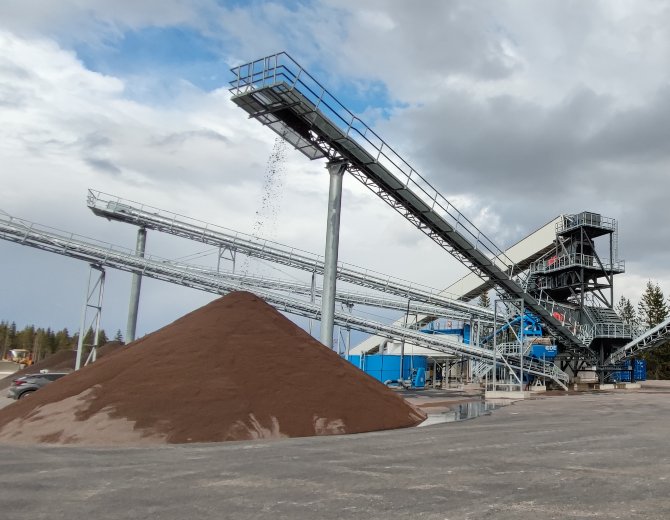
The Results
The plant produces 2 sands in 0-2mm and 2-4mm fractions and 4 gravels in sizes 4-8mm, 8-11mm, 11-16mm and 16-22mm. The 0-4mm sand goes mostly into asphalt products, mostly for road gritting in winter while the 0-2mm is in-spec manufactured sand for concrete production.
The new washing facility means that Feiring will be able to utilise 100% the extracted material and recover stockpiles of old residues from crushing operations. It makes it possible to produce an industrial sand that has the same or even better properties as natural sand for use in the concrete industry, the biggest user of natural sand. It’s a win-win both in terms of resource use and the emissions associated with transport.
In addition, the CDE washing plant has boosted production on site and improved sand quality, opening up new business opportunities for Feiring, including a contract with a nearby concrete plant to supply industrial sand and the supply of sand to asphalt producers who would normally have to buy natural sand.